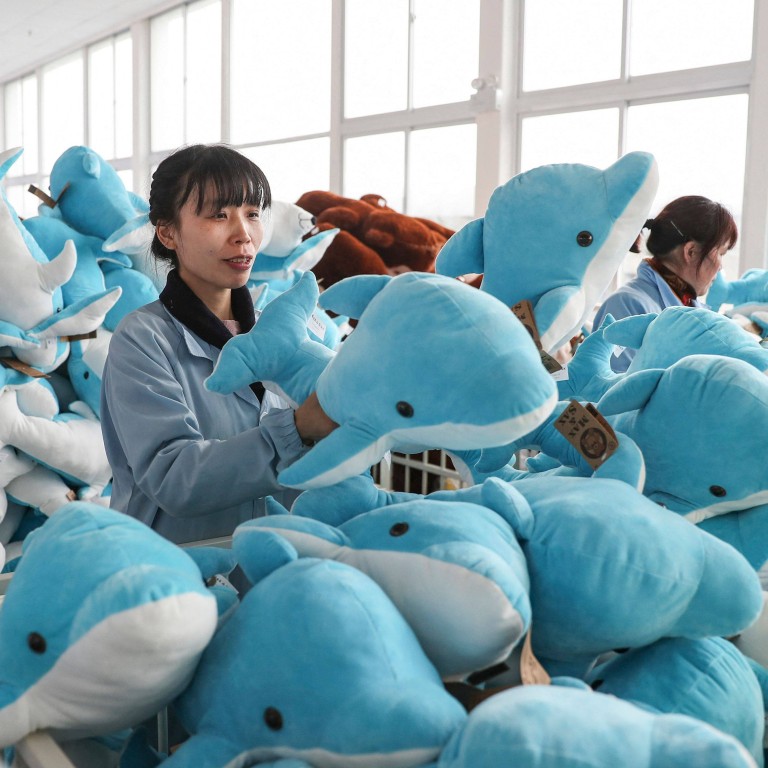
By all means, save Christmas – but don’t blame the global supply chain
- As logistical chaos threatens Christmases across the US and UK, the lesson is not that the global supply chain should be dismantled but that, in modern manufacturing, small hiccups can cause big disruptions
Others have warned that the final nail is being rammed into the coffin of the long, complex supply chains that have fuelled global growth over the past four decades.
Certainly, the short-term disruption is extraordinary. But is it really likely to lead in the medium term to structural changes in the way we trade? My guess is no.
There is no doubt that the perfect storm of disruptive forces has been shocking, and would have been hard to anticipate even as Covid-19 engulfed the global economy in the first half of last year.
Who would have foreseen the whipsaw effects as economic activity first crashed in the second quarter of last year, then rallied more strongly than anyone would have dared predict? The World Trade Organization says global trade collapsed by 5.3 per cent last year, and will rebound by 10.8 per cent this year.
China’s exports are up by about a third so far this year, according to WTO data, and Asia’s exports have rallied to 15 per cent above 2019 levels, before the pandemic hit. Even US and European exports are back on par with 2019.
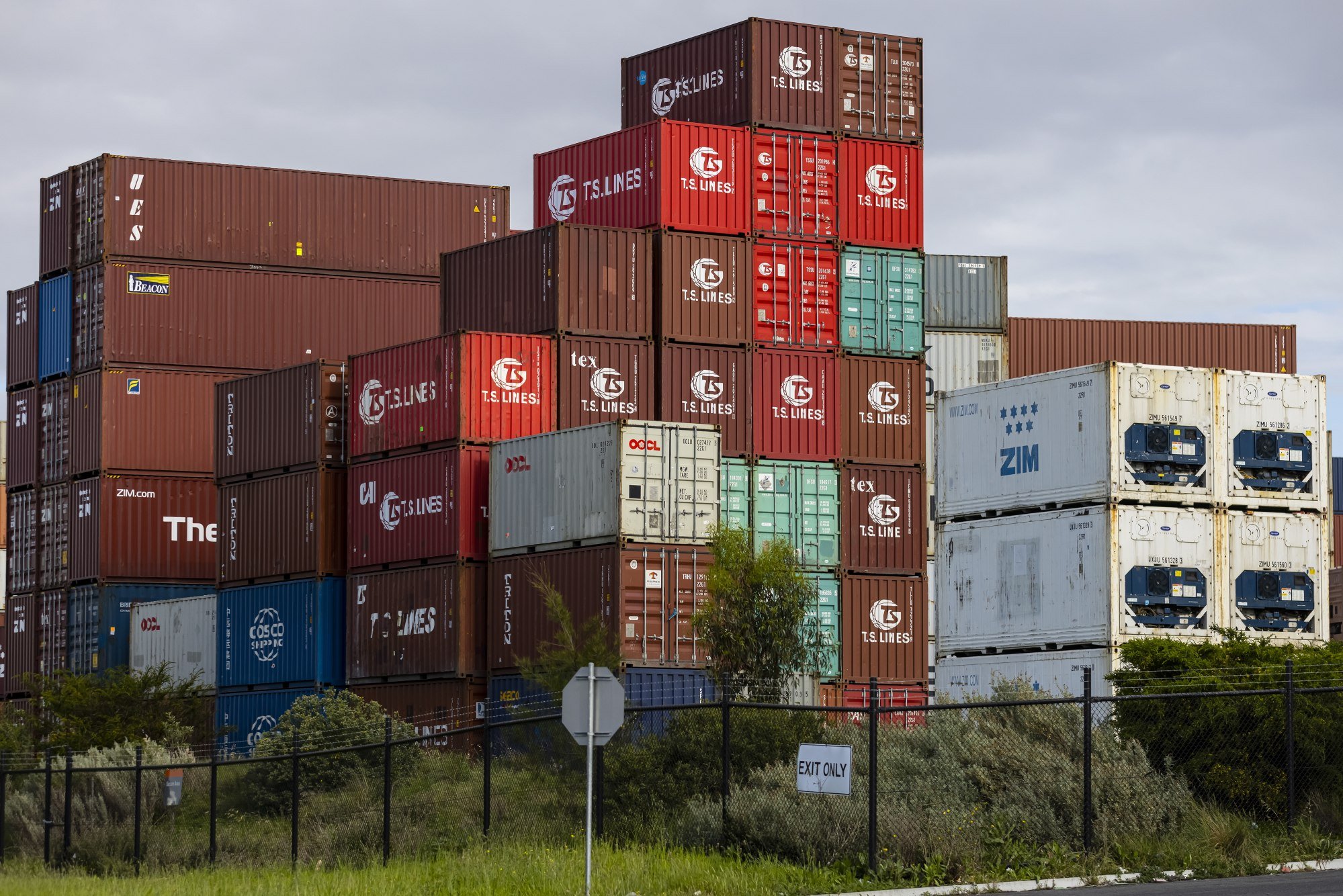
So the raw trade data contradicts suggestions that trade has been suppressed or supply chains dismantled. Few predicted America’s rapid and powerful consumer boom as money saved from restrictions on travel and dining was diverted to online consumption.
US-China trade still holds the key to global recovery
I am reminded of the 1958 essay “I, Pencil: My Family Tree as told to Leonard E. Read”, which reads: “Pick me up and look me over. What do you see? Not much meets the eye – there’s some wood, lacquer, printed labelling, the graphite lead, a bit of metal and an eraser.”
But the narrator, the pencil, then reminds us that the cedar wood needed saws, motors and railways; that the graphite came from Ceylon (now Sri Lanka) and was mixed with Mississippi clay, sulphuric acid and animal fats; that the eraser needed rapeseed oil, sulphur chloride and Italian pumice. In 1958, even with something as simple as a pencil, manufacturers needed long and complex supply chains.
Today, Apple needs around 200 suppliers across 800 production facilities worldwide. BMW has more than 100 parts suppliers, just 43 per cent of which are based in Germany. Tesla’s Model 3 needs 10,000 unique parts to be complete.
The lessons from the current supply chain crisis suggest not that they should be dismantled, nor that everything be made at home, but that the complexity of modern manufacturing is such that even modest disruptions can lead to things going wrong on a very large scale.
There may be a case for what Barry Lynn, head of the anti-monopoly Open Markets Institute, calls the “rule of four”: no more than 25 per cent of any crucial supply should be sourced from one place.
Mass panic behind global supply chain crisis
It is true that the Long Beach and Los Angeles ports, which handle around 40 per cent of US cargo shipping imports, will remain a liability as long as they resist the global trend towards 24/7 port operations, but this is not the lone cause of America’s bottlenecks.
A shortfall of around 60,000 truck drivers does not help. Nor that so many retailers, rushing to build inventory ahead of Christmas, means warehouses have little space left for the cargo coming in.
As a Financial Times editorial reminded us last week, the crisis has much to do with the annual Christmas challenge of “pushing the pig through the python” – accommodating the annual festive consumption surge through a transport system built for the quieter months of the year. We may need to wait until January before long-term lessons will be learned. Meanwhile, a slimmed-down Christmas may be in store.
David Dodwell researches and writes about global, regional and Hong Kong challenges from a Hong Kong point of view
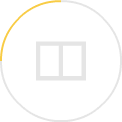