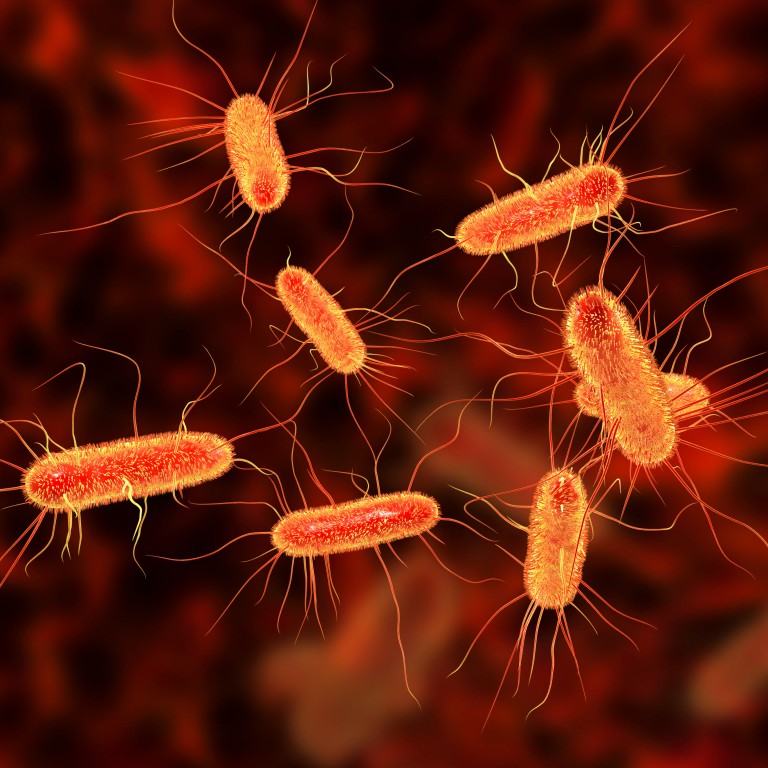
US start-up’s bacteria can convert gas emissions from Shougang’s Beijing steel mills into ethanol
- LanzaTech is helping its partner Shougang Group build two bioreactors to make ethanol from gases emitted by the Beijing-based steel maker’s plants
- Microorganism-enabled conversion of simple compounds into complex industrial material building blocks has reached early commercialisation, according to IDTechEx
Technology that uses microorganisms to turn carbon emissions into raw materials is edging closer to commercialisation as production is scaled up to cut costs, according to industry experts.
Some start-ups have demonstrated the viability of their technology through pilot plants by reducing the use of virgin fossil fuel resources to produce fuels and industrial materials.
The US’ LanzaTech is one such promising start-up. The Chicago-based company has developed technology that uses bacteria to convert carbon monoxide into ethanol. Ethanol can be blended with petrol for use as motor fuel, or as a feedstock for making chemicals with applications from garments to packaging.
“We are not just trying to decarbonise industry, brands and their products, we are [saying] there is already enough carbon above the ground [that we] can use to make things for our daily lives that normally comes from fossil carbon,” CEO Jennifer Holmgren said.
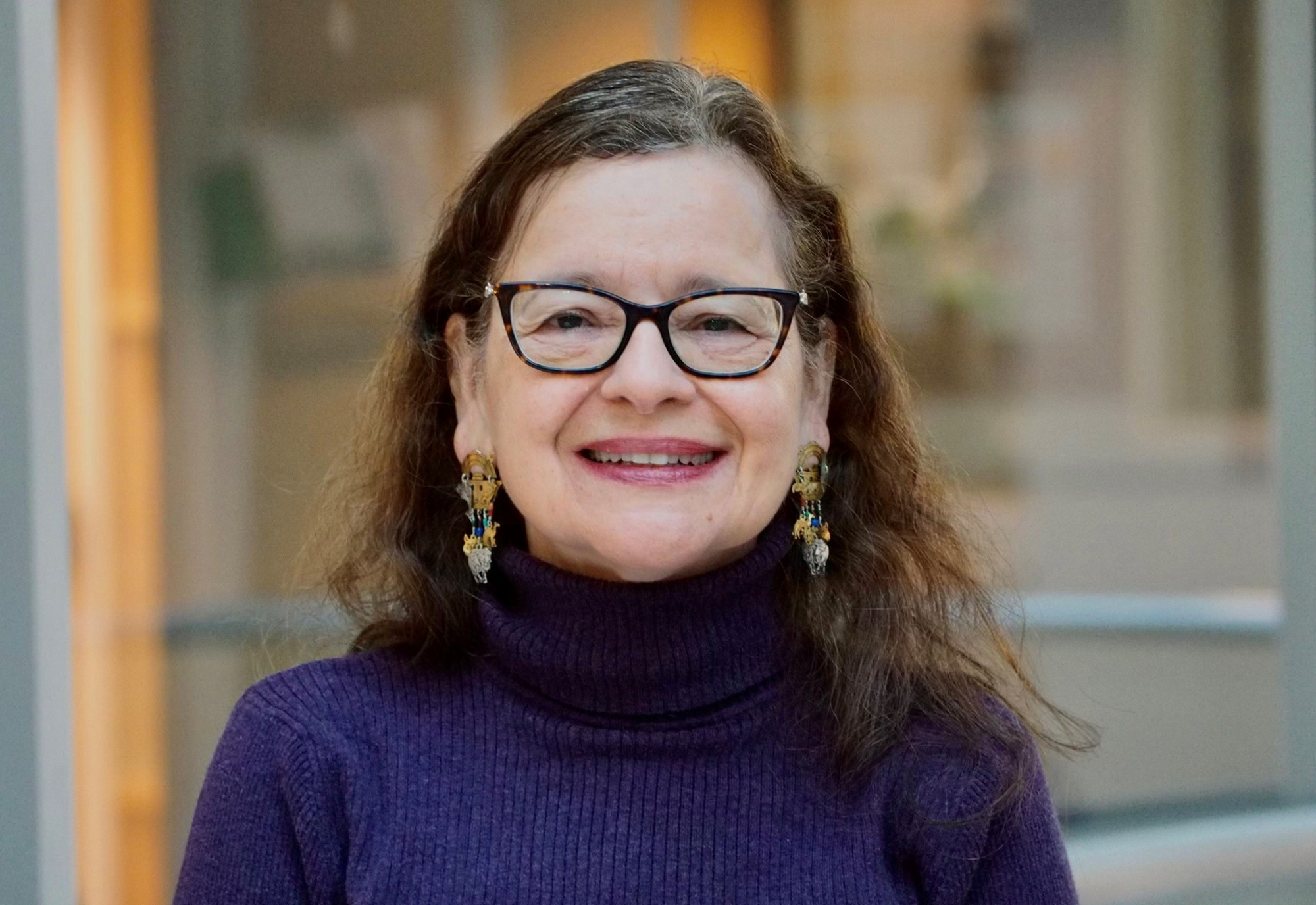
After 14 years of research, LanzaTech has helped its partner Shougang Group build two bioreactors to make ethanol from gases emitted by the Beijing-based steel maker’s production facilities.
LanzaTech’s “gas fermentation” technology is similar to brewing. Instead of using yeast that eats sugar to make alcohol, it uses a bacteria to “eat” waste carbon to make ethanol.
Another 14 LanzaTech facilities financed by other partners with a total capacity to capture one million tonnes of carbon gases annually in the US, India, Canada, Europe, South Africa and Australia are in various stages of engineering and construction.
Costing US$50 million to US$100 million each, they turn carbon gases extracted from industrial, municipal and agricultural wastes into ethanol, Holmgren said.
Such recycled carbon gas-derived materials have found their ways in small quantities in apparel made by Zara and Lululemon, Danone food packaging and Coty perfume.
Microorganism-enabled conversion of simple compounds into more complex industrial material building blocks has reached early commercialisation, said UK-based market research firm IDTechEx.
“Recent advances in genetic engineering and process optimisation have led to the use of microorganisms in synthetic biological routes to convert carbon dioxide into chemicals, fuels and even proteins,” it said in a statement on Tuesday.
California-based start-up Newlight Technologies uses methane and carbon dioxide-eating microorganisms to make a “carbon negative” biodegradable material called polyhydroxybutyrate to replace plastic and leather.
Last month, it launched a coating for moisture and grease-resistant paper products such as coffee cups and takeaway containers.
Since production began in May 2018, LanzaTech has produced nearly a million tonnes of ethanol, preventing 130,000 tonnes of carbon dioxide emissions.
Due to limited financial resources, it has so far primarily licensed its technology to partners. After recent rounds of fundraising, it is seeking to invest in some of their projects.
It has raised over US$500 million since its inception, Holmgren said. Its shareholders include steel titans ArcelorMittal and China Baowu Steel Group, chemicals giants BASF and China Petrochemical Corp, besides investment banking and management firm China International Capital Corp and Chinese conglomerate Citic.
LanzaTech has enlisted Switzerland-based The Roundtable on Sustainable Biomaterials to certify the sustainability of the plants and track the materials’ movement, so that its licensing partners can charge a premium compared to fossil fuel-derived ethanol to reflect the climate benefits.
The company has nearly 1,100 patents and 475 pending applications globally related to its fermentation processes.
Still, for the nascent sector, viability questions such as financial and other barriers to commercialisation and whether the technologies can be scaled up to address climate change meaningfully need to be addressed, IDTechEx said.
“Not all carbon dioxide utilisation pathways are equally beneficial to climate goals and not all will be economically scalable,” it said.
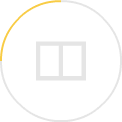