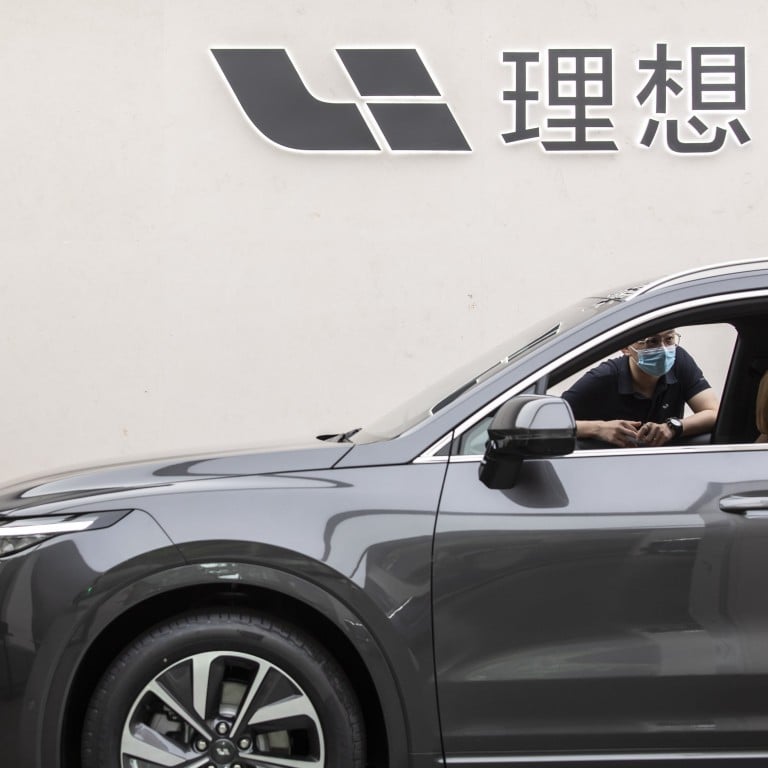
Tesla challenger Li Auto expects bumpy road ahead, as Shanghai lockdown snarls supply chains
- The electric vehicle start-up expects to ship up to 33.8 per cent fewer cars in the second quarter compared to the first three months of the year
- Covid-19 lockdowns in Shanghai and a major car production base in Jilin province have exacerbated a bottleneck in automotive supplies
Li Auto, the Chinese smart electric vehicle (EV) start-up, has forecast a sharp fall in its deliveries in the second quarter, as strengthened virus control and prevention measures further constrain the supply chain.
The Beijing-based rival to Tesla expects to ship between 21,000 to 24,000 vehicles from April to June, compared to 31,716 in the first quarter – representing a decline of between 24.3 per cent and 33.8 per cent.
“While the recent pandemic resurgence and associated supply-chain interruptions have been challenging for our industry, and uncertainty remains in the near future, we are confident of the resilience of our organisation,” Li Xiang, co-founder and CEO of Li Auto, said in a statement on Tuesday.
April deliveries at Tesla’s Chinese rivals fall as Shanghai locks down
The company’s bearish forecast came after Tesla reported sales of 10,757 units in April, down 84 per cent from a month earlier.
Li Auto reported on Tuesday a net loss of 10.9 million yuan (US$1.6 million) in the first three months of the year, falling short of market expectations of a quarterly profit.
The gross margin of its vehicles increased slightly to 22.4 per cent in the same period, compared to 22.3 per cent in the last quarter of 2021 and 16.9 per cent a year earlier.
Guangzhou-based Xpeng Motors and Shanghai-headquartered Nio, Tesla’s two other Chinese challengers, have yet to publish their earnings for the first quarter.
In February, before the current Covid-19 outbreak in Shanghai, the China Passenger Car Association had predicted an 84 per cent yearly jump in total sales of new energy vehicles (NEVs) – comprising pure electric, plug-in hybrid and fuel-cell cars – to 5.5. million units this year.
The EV industry, considered a bright spot in the mainland’s slowing economy, has been grappling with a severe shortage of automotive chips and batteries since last year, due to the lack of adequate production capacity at component suppliers to support its sizzling growth.
“Lockdowns have forced thousands of vendors to suspend production over the past two months and it will take time for them to get production facilities running at full capacity,” said Cao Hua, a partner at private-equity firm Unity Asset Management. “All the EV companies are doing now is to secure as many key components as needed to build up an inventory that can support the operations of their assemblies.”
Li Auto, with its major assembly based in Changzhou, Jiangsu province – around 160 kilometres (99 miles) from Shanghai – is among the main victim of a broken automotive supply chain and disrupted logistics system.
Last month, the company delivered 4,167 units to buyers, down 62.3 per cent from March.
Shanghai, China’s commercial and financial capital, imposed a citywide lockdown on April 1, and authorities have yet to provide a time frame for lifting the stringent measures.
Tesla’s Shanghai plant hits snag as lockdown strains supply chain
Tesla’s Gigafactory 3 in Shanghai produced 50,000 fewer vehicles than usual due to a suspension in operation between March 28 and April 18. The plant resumed production on April 18 under a “closed-loop” system that has workers sleeping on site to avoid physical contact with the outside world.
Despite the measure, the factory has shut down at least part of its assembly line since Monday due to a supply-chain breakdown.
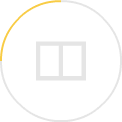