Pharmapack adds inventive solutions to sterile pharmaceutical packaging
Company specialising in blow-fill-seal technology is open to possibilities in product developments and new markets
[Country Business Reports interviews and articles by Discovery Reports www.discoveryreports.com]
Pharmaceutical products require special packaging. They must be kept sterile and free from contamination. Thanks to blow-fill-seal (BFS) technology, containers can be formed, filled and sealed in one continuous process in a controlled environment.
One company specialising in BFS is Pharmapack, Japan’s leading pharmaceutical products contract manufacturer. Founded in 1965 and a member of the Hanshin Group, it takes pride in its mastery of BFS technology. Besides research and development support, Pharmapack uses the plastic parts manufacturing expertise of a Hanshin subsidiary – Hanshin Kasei – to enhance its service offering. These capabilities help make Pharmapack a key player in the industry.
“By combining our know-how with Hanshin Kasei’s, we can develop products which other companies cannot,” says Junichi Takata, president of Pharmapack. The company produces inhalation solutions, eye drops, disinfectants, nose drops and enema in its 14,000 square metre plant. It can create products befitting customers’ needs, for example, a casing with plastic parts for single-dose eye drops employing a unique opening method.
Pharmaceuticals BFS manufacturing is a niche sector requiring constant technological advancements
Pharmapack has initiated activities to increase market share and global competitiveness. In 2016, it participated in the BFS International Operators Association meeting as a major sponsor. It expanded the plant’s quality evaluation area last year, and started constructing a new factory set to be finished this year to increase its capacity by 20 per cent. Pharmapack employs quality improvement strategies to be on par with good manufacturing practice (GMP) standards.
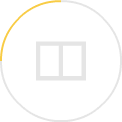