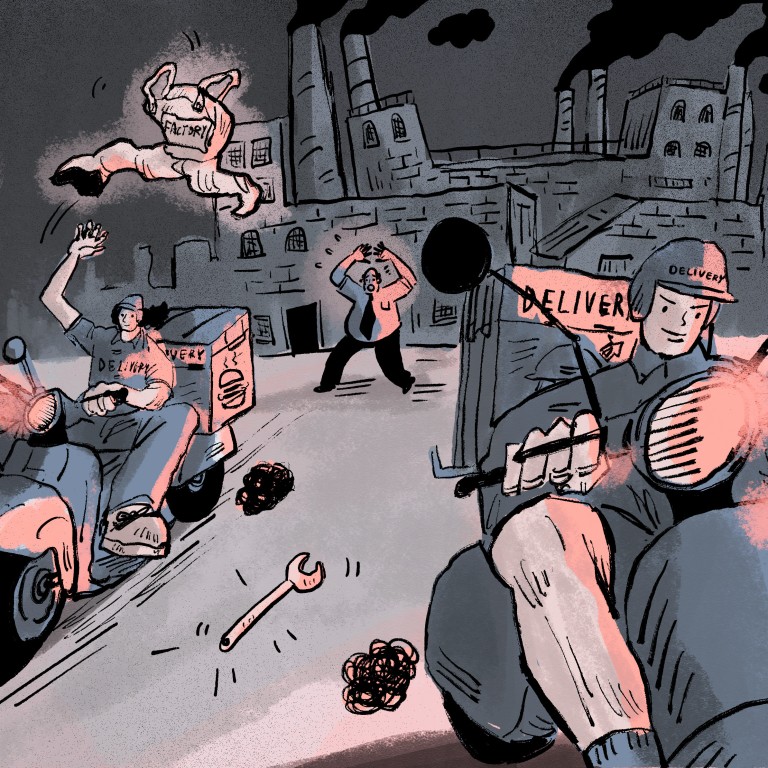
China’s migrant workers are shunning factory jobs, and manufacturers are getting desperate
- Economists say China has reached a stage of economic development where young people are less inclined to take low-wage factory work, as better options are available
- Automation is helping manufacturers offset labour losses, but a lack of skilled engineers and other specialists is also slowing the development of advanced technologies
China’s young migrant workers are turning up their noses at humdrum factory jobs – a line of employment that previous generations were content with. Instead, many are opting to join the nation’s army of delivery workers, lured by better pay and more flexible hours.
“An internship at a factory can’t teach you anything,” said Liao Yong, a 19-year-old delivery driver in Beijing, where the job can easily bring in 15,000 yuan (US$2,350) a month – or about twice what some factory workers make on the low end.
“For seven or eight hours a day, you just keep repeating one job over and over again. There’s no room for me to improve my skills and advance. But delivery is more fun, and I get to see different things and meet different people.”
Young migrant workers nowadays want to have a life … working as a waiter at a restaurant is more appealing than a factory job
But for many of China’s young migrant workers, that’s a big ask. To them, the factory jobs their parents worked to pay for their rural homes are less appealing, even without considering new opportunities and the boom in urban delivery services.
“I have more liberty with my time, and I can make more money if I work more,” said 21-year-old Wang Juncheng, another delivery driver in Beijing.
This sort of reluctance to take factory work has become increasingly common across China’s migrant groups, according to Zhuang Bo, a China economist at investment firm Loomis, Sayles & Company.
“Young migrant workers nowadays want to have a life, and they hope to live and stay in the city,” Zhuang said. “And for many of them, working as a waiter at a restaurant is more appealing than a factory job.”
By 2025, nearly 30 million manufacturing jobs in the country will go unfilled, according to the Ministry of Human Resources and Social Security, whose surveys also showed that about half of the 100 jobs facing the most severe labour shortages were manufacturing jobs, in the second half of last year.
Around 44 per cent of industrial companies last year said hiring difficulties were atop their challenges, according to the National Bureau of Statistics.
A rising average wage in China, coupled with an expanding service sector, gives Chinese workers more job options that pay better, said Larry Hu, chief China economist at Macquarie Group.
“The reason China became the world’s factory and took in many offshored factories from developed countries was that young people in those countries didn’t want to work [low-paying] assembly jobs any more,” Hu said. “China has now reached this stage, too, and that is the result of economic development.”
Rise of the machines: China’s struggling industries embrace automation
In the face of these headwinds, along with mounting labour costs and uncertainties, China has one of the world’s most ambitious automation plans.
According to its five-year plan for smart-manufacturing development, China aims to digitise 70 per cent of domestic manufacturers by 2025.
Experts have long debated whether China should revamp its industrial sector by removing or offshoring lower-end manufacturing. Some contend that this would increase blue-collar salaries and help solve the labour-shortage problem.
“As long as factories can provide a better quality of life, such as higher wages and housing, labour shortages can be mitigated,” Zhuang said. “A labour shortage is a relative problem – factories have difficulty hiring workers only at the current [low] salaries.
“Some factories provide long-time workers with housing benefits, help with [obtaining] local residency, and with their children’s school – these factories have no such worries at all.”
And it’s not just about struggling to recruit assembly-line workers. Manufacturers are decrying a shortage of skilled workers, such as engineers, in the smart-manufacturing sector. Under the government’s guidance, China’s higher education system has failed to cultivate and deliver talents that the markets are desperate for.
Vertiv, a global provider of critical digital infrastructure solutions, is among those that have been ramping up recruitment in China over the past two years. A total of 30 fresh college graduates were hired in 2020, more than 130 were hired in 2021, and Vertiv will hire more than 300 recent graduates this year, according to staff.
“We are extremely in need of new people,” said Duan Bixin, a 24-year-old project manager at Vertiv, adding that universities are slow to set up majors in areas of market demands, such as new energy and carbon neutrality.
In smart manufacturing, jobs such as data governance, software architecture, data engineering, intelligent engineering and robotic engineering are in high demand, according to a survey published last year by China International Intellectech, a think tank.
China’s delivery drivers along for the ride as economy gathers steam
“The mismatch between education and market demands has existed for years and became more pronounced in the past few years,” said Wang Dan, chief economist at Hang Seng Bank China.
“Students are majoring in homogenised fields, such as economy, finance and computer science. Few of them are directly suited for manufacturing.
“Education, or rather training needed for the development of manufacturing, requires a different system. Unskilled workers can take on a low-end factory job and receive training on the spot, but the talents needed in high-level manufacturing require many years of hands-on training.”
And that sort of training, Wang said, is hard to come by in China.
Beijing aimed to address this way back in 2008, by setting up the Thousand Talents Plan – a state-backed recruitment drive to lure foreign talents and Chinese scholars from overseas, particularly in science and technology, with cash grants to fund their research and living costs.
Has one philosophy student changed the face of migrant workers in China?
But the controversial plan came under heavy scrutiny, including from the US government, for allegedly using American research and expertise to give China’s economy and military a boost. And online references to the plan started being deleted in October 2018, according to a 2019 report by the US Senate’s Permanent Subcommittee on Investigations.
Noting the importance of being able to recruit high-level talent from overseas, Wang pointed out how geopolitical tensions in recent years have hindered the flow of talent into China. And she said that cultivating domestic talent will be a slow process, given limited funding and resources.
Despite China’s push for vocational education to equip teenagers and young adults with advanced technical skills, no benefits are expected in the short term, and the pool for such talent looks to remain shallow for the time being.
Solving the shortage of manufacturing workers [in China] requires more investment in research and development; increased manufacturing profits; better wages and worker benefits; and improved training programmes
But Wang is sceptical of the endeavour, as there have been few successful precedents.
“The operational costs are too high. Without government subsidies, it is difficult for private universities to be sustainable. Cao Dewang and Jack Ma are exceptions – as famed entrepreneurs, they have the financing ability. But in China, a more practical way is for universities to work with local governments,” she said.
Germany serves as an example for China to move up the value chain by developing an advanced manufacturing industry and cultivating skilled workers.
“In Germany, workers enjoy competitive benefits and job security without being affected too much by the global economic cycles, and this is mainly because Germany’s industrial products are of high value,” said Zhuang from Loomis, Sayles & Company.
“Therefore, solving the shortage of manufacturing workers requires more investment in research and development; increased manufacturing profits; better wages and worker benefits; and improved training programmes.”
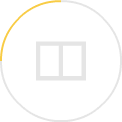