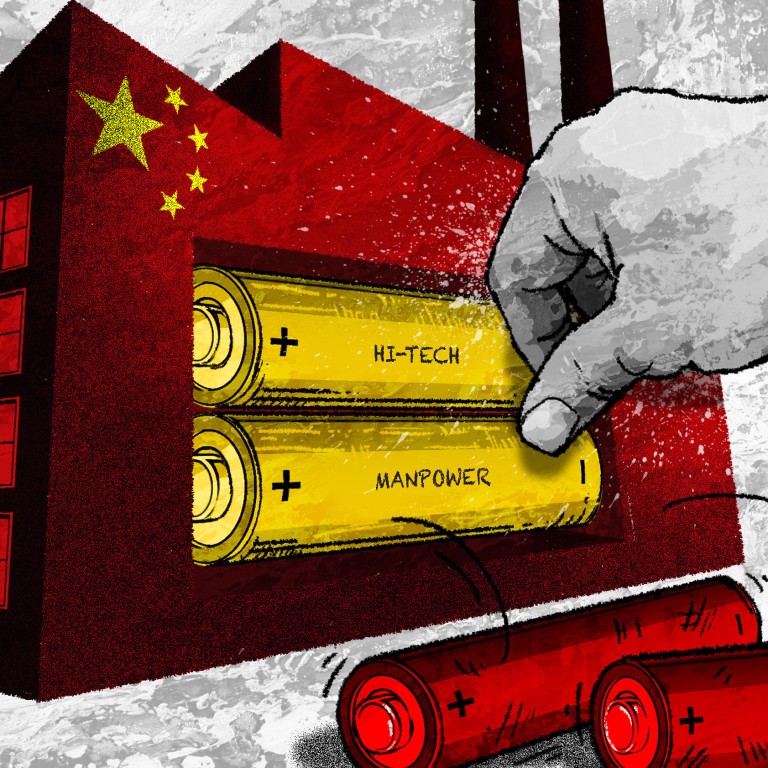
China’s factories try to manufacture their way out of a shortage of both jobs and hi-tech
- Manufacturers and others are pointing to a growing mismatch between the jobs young people are looking for and the jobs that are in dire demand
- Finding skilled workers has become so costly that the roughly 10,000-yuan cost of replacing them recently trended on social media
The world’s factory is in a bind, facing a number of internal and external challenges that are exposing and accentuating ways China needs to improve if it hopes to retain an edge in manufacturing amid technological restraints and demographic shifts.
At a manufacturer in northern China’s Tianjin, a piece of coated metal is hoisted into a blazing-hot gas furnace that must be precisely controlled. The exactness of this carburising step is vital, as it can determine if the part – in this case, industrial gearboxes – will last for 10 years or 50 years.
However, the data being relayed from inside the furnace is not handled on-site. Instead, it is transmitted all the way to Germany, where engineers monitor the highly technical process from the headquarters of the plant’s owner.
Without access to core technology, which increases the added value of such products, the Chinese side is responsible for purely operating the machine.
The supply of a large number of key core technologies and middleware in China’s manufacturing sector is heavily dependent on foreign countries
And therein lies a critical hurdle facing China’s manufacturers – bridging technical gaps in an increasingly competitive global trade environment.
“The supply of a large number of key core technologies and middleware in China’s manufacturing sector is heavily dependent on foreign countries,” a Zheshang Securities report said last March.
A second major hurdle involves manpower. While China continues to offer relatively cheap labour, a comprehensive industrial and supply chain, and policy support, demographic and societal changes have created a shortage of skilled blue-collar workers.
While automation is becoming more ubiquitous in manufacturing, such technical experts remain essential in operating the machines and repairing them – from digital coding to physical components.
And if factories are unable to find these skilled workers, the resulting labour crunch could force companies to cut orders. On a nationwide scale, this could have far-reaching ramifications as China strives to reinvigorate its economy after three difficult years under zero-Covid.
A lot of people are looking for a job, but at the same time, it is difficult for us to find qualified, skilful workers
According to a worker at the Tianjin-based manufacturer, which agreed to give the Post a tour of the facility under the condition that the firm not be named for this report, the company is among those facing growing difficulties in hiring skilled factory hands.
This reflects a broader trend in China that has resulted in a mismatch between the jobs young people are looking for and the jobs that are in dire demand.
Even as 95 per cent of the country’s vocational graduates are able to land jobs soon after graduation, manufacturers have been reporting hardships in hiring blue-collar workers, especially skilled ones.
The issue became so widely discussed online recently that a trending topic on Weibo – China’s Twitter-like platform – was about how the cost to find and hire such workers exceeds 10,000 yuan (US$1,450).
“A lot of people are looking for a job, but at the same time, it is difficult for us to find qualified, skilful workers,” said Cindy Zheng, CFO of the Wago Electric Tianjin company, an electrical connector manufacturer that is also headquartered in Germany.
China must ‘tolerate failure’ in science and tech to close gap with US
Speaking on March 10 at a European Chamber of Commerce event in Tianjin, Zheng said her Tianjin operation struggled to recruit skilled blue-collar workers in a short time last year when they needed to eliminate a backlog of orders resulting from years of coronavirus-induced lockdowns.
Young people these days like to work flexible gigs, such as delivery jobs, while 20-something young workers tend to shy away from working at a manufacturing company, she added.
But this type of trend, she said, is “also very risky”, particularly in terms of how it affects China’s “Made in China 2025” plan – a government strategy to upgrade hi-tech industries to Western levels while reducing China’s dependency on imports.
“We are talking more about high-end manufacturing and smart manufacturing,” Zheng said. “That means we need a large number of skilful blue-collar workers to respond to this change and to become a high-end [research and development] manufacturing centre.”
It’s vital … for people to know that blue-collar workers are not the same as 50 years ago
She pointed out how it was particularly hard to find workers to operate computerised numerical control (CNC) machine tools, as such staff must be equipped with strong vocational skills. CNC manufacturing uses preprogrammed computer software to control machine tools.
By 2025, nearly 30 million manufacturing jobs in China will go unfilled, accounting for nearly half of all jobs in the sector, according to the Ministry of Human Resources and Social Security, whose surveys also found that about half of the top 100 jobs facing the most severe labour shortages were in manufacturing in the second half of last year.
The dearth of skilled engineers is compounding the pressure on manufacturers, and the shortage is stymieing China’s ambitious push to bolster its intelligent manufacturing sector, which Beijing expects will help drive the nation’s economy in the future.
“The government should closely work with the industry and industry associations to know the perspective and trends of our manufacturing companies,” Zheng said, adding that more vocational schools should be opened to bolster the talent pool and meet the growing demand for skilled workers.
If workers’ salaries keep rising, costs go up, and that could create a potential crisis in the future
Christoph Schrempp, general manager of the Airbus Completion and Delivery Centre in Tianjin, said the central government should also provide highly skilled blue-collar workers with more room for career advancement, more social class and greater public respect, which will in turn would benefit all of society.
“It’s vital to change the public perception, and for people to know that blue-collar workers are not the same as 50 years ago,” he said.
Elsewhere in Tianjin, the owner of a shipbuilding company is worried about not being able to hire sufficient staff to meet demand.
Fewer and fewer young people are willing to work in his shipyard, he explains, adding that he has had to raise wages to keep up with orders.
“If workers’ salaries keep rising, costs go up, and that could create a potential crisis in the future,” said the owner surnamed Mu, who spoke on condition of anonymity. “If a company can’t make a profit, their business could face potential shrinkage, and workers might not be able to find jobs – this is a vicious cycle.”
Although China is pushing for vocational education among students to cultivate talent with high-end technical skills, the fruits of that labour will not come until later. Thus, the pool for such talent looks to remain shallow in the near term.
According to a report on blue-collar employment, published in late December, China had more than 400 million blue-collar workers in 2021, accounting for more than half of China’s working-age population. But a large segment among those millions does not possess the necessary skills required by China’s upgraded and more technologically advanced manufacturing sector.
Structural problems also still stand at the heart of China’s many employment-related quandaries, including the mismatch between young jobseekers unwilling to work blue-collar jobs; companies in the industrial and construction sectors desperate for workers; and high youth-unemployment levels.
The jobless rate for the 16-24 age group in February remained at an elevated level of 18.1 per cent, up from 16.7 per cent in December. The broader urban surveyed unemployment rate, meanwhile, stood at 5.6 per cent in January and February, up slightly from 5.5 per cent in December.
Is China’s vocational training fit for its advanced manufacturing ambitions?
At the recently concluded “two sessions” parliamentary gatherings in Beijing, representatives of China’s legislative bodies suggested that authorities roll out more support measures to help innovate hiring platforms and otherwise make it easier to match potential workers with employers.
Meanwhile, technological “choke points” continue to have an outsized impact on Chinese operations, further affecting jobs as Western nations employ containment measures to impede China’s technological prowess.
In 2018, a report identified “choke point” technologies that foreign countries could use to contain China. Based on statistics compiled by Science and Technology Daily, the official newspaper of the Ministry of Science and Technology, the list named chips, aviation, software, tactile sensors, heavy-duty gas turbines, microspheres, lidar, medical imaging equipment, and a range of other industries.
Also that year, the Ministry of Industry and Information Technology published the results of a survey showing that 32 per cent of key materials were completely inaccessible among more than 130 types of key basic materials used by more than 30 Chinese companies. Also, more than half of key materials relied on imports, and 95 per cent of high-end chips for most computers and servers relied on imports.
Fast forward five years, and there have not been any updated figures nor substantial technological breakthroughs that address these “choke points”, a term that still makes headlines in trade and manufacturing circles.
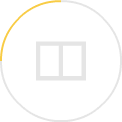