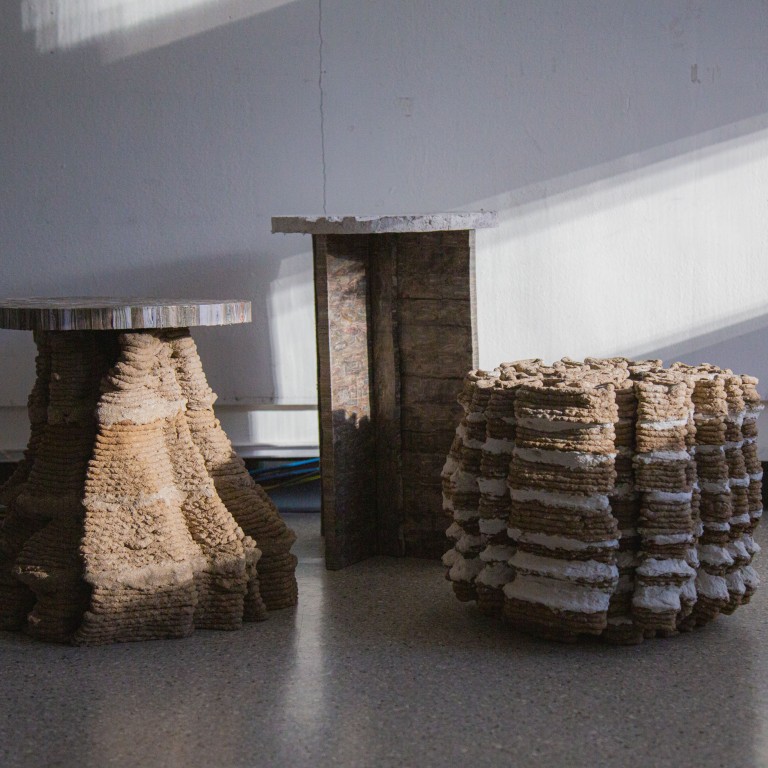
Upcycled waste: sustainable furniture and homewares made from eggshells, earth, paper, fruit peel – even blood
- In Hong Kong, designers like Niko Leung are seeking out ways to use waste materials to craft sustainable homewares, furniture and construction materials
- Tests are being done on everything from soil to loofah, egg and oyster shells, durian skin and even blood powder, a slaughterhouse by-product
Most people walk past construction sites without paying them any attention. Not Niko Leung Hong-ken.
Curious about what lies beneath, the Sai Kung-based product designer hunts down subsoil from different parts of Hong Kong from which to craft sustainable homewares.
Leung’s two years working at architectural manufacturing company Royal Tichelaar Makkum in the Netherlands fuelled her desire to research purposeful reuse of discarded soil from building sites.
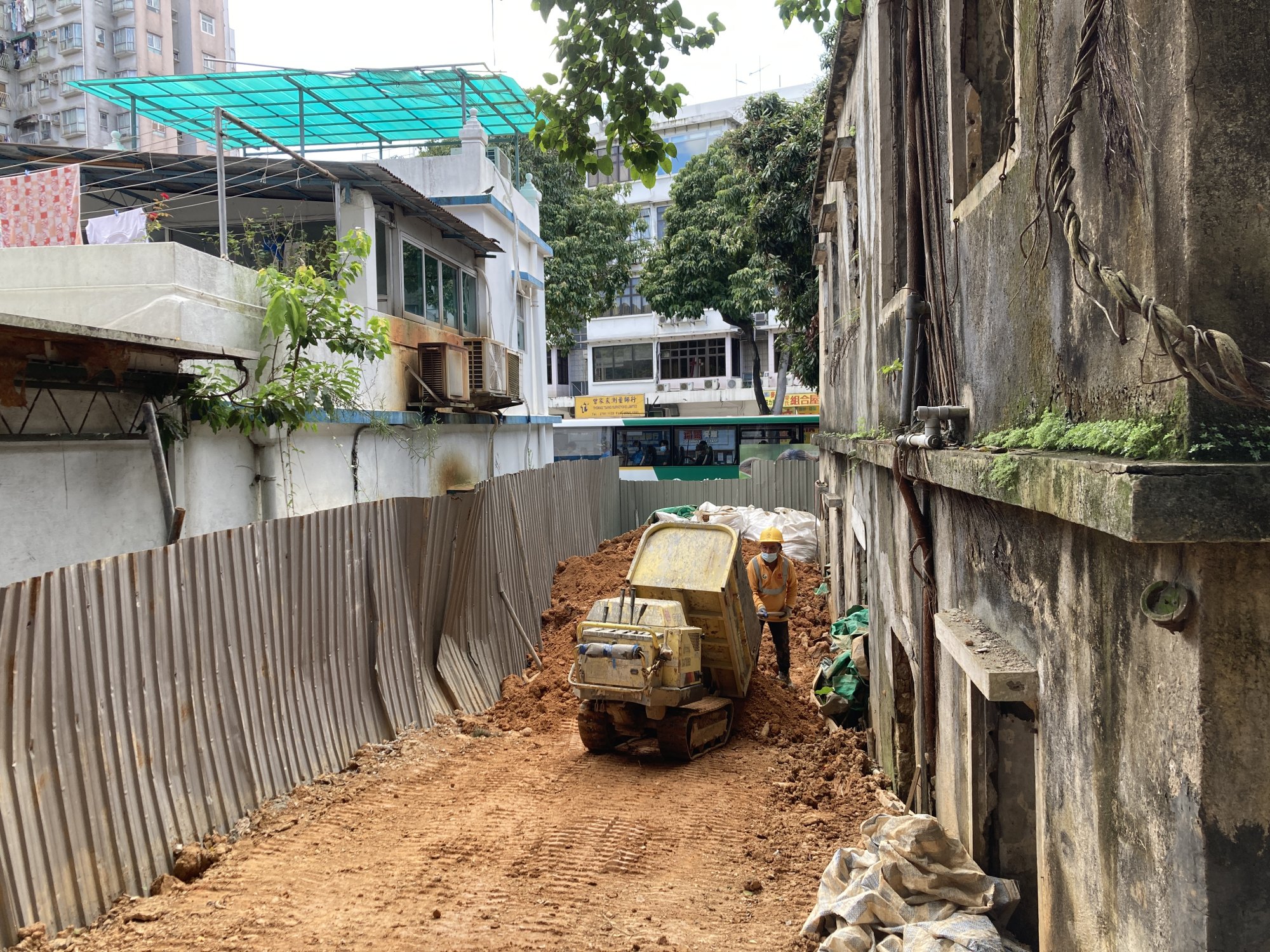
In 2015, she returned to Hong Kong and, in 2021 – upon securing funding from Design Trust – she co-founded Hong Kong Soil with architectural designer Loky Leung Lok-kwan.
“It’s difficult to get the material,” Leung explains. “Dirt is low cost and widely available, but to recycle it for non-builders’ work is nearly unprecedented here in Hong Kong.” Nevertheless, the partners were able to source about 15 tonnes (16.5 tons) with which to experiment.
Not all of the raw material is suitable. A good soil for rammed earth requires the right ratio of sandy loam and gravelly clay. For functional ceramics, mainly clay is preferred.
Plus, it is hard to find “clean” earth in Hong Kong, because many sites have been previously developed or are on reclaimed land.
I very much see the future economic and cultural significance earth could bring
Putting a grid over a map of Hong Kong, the partners plotted potential sites within a 5km (3.1 mile) radius, dug below the surfaces of the areas, then analysed the samples.
Apart from physical composition, there are distinct variances in colour and texture in soil from the New Territories, Hong Kong Island and Kowloon.
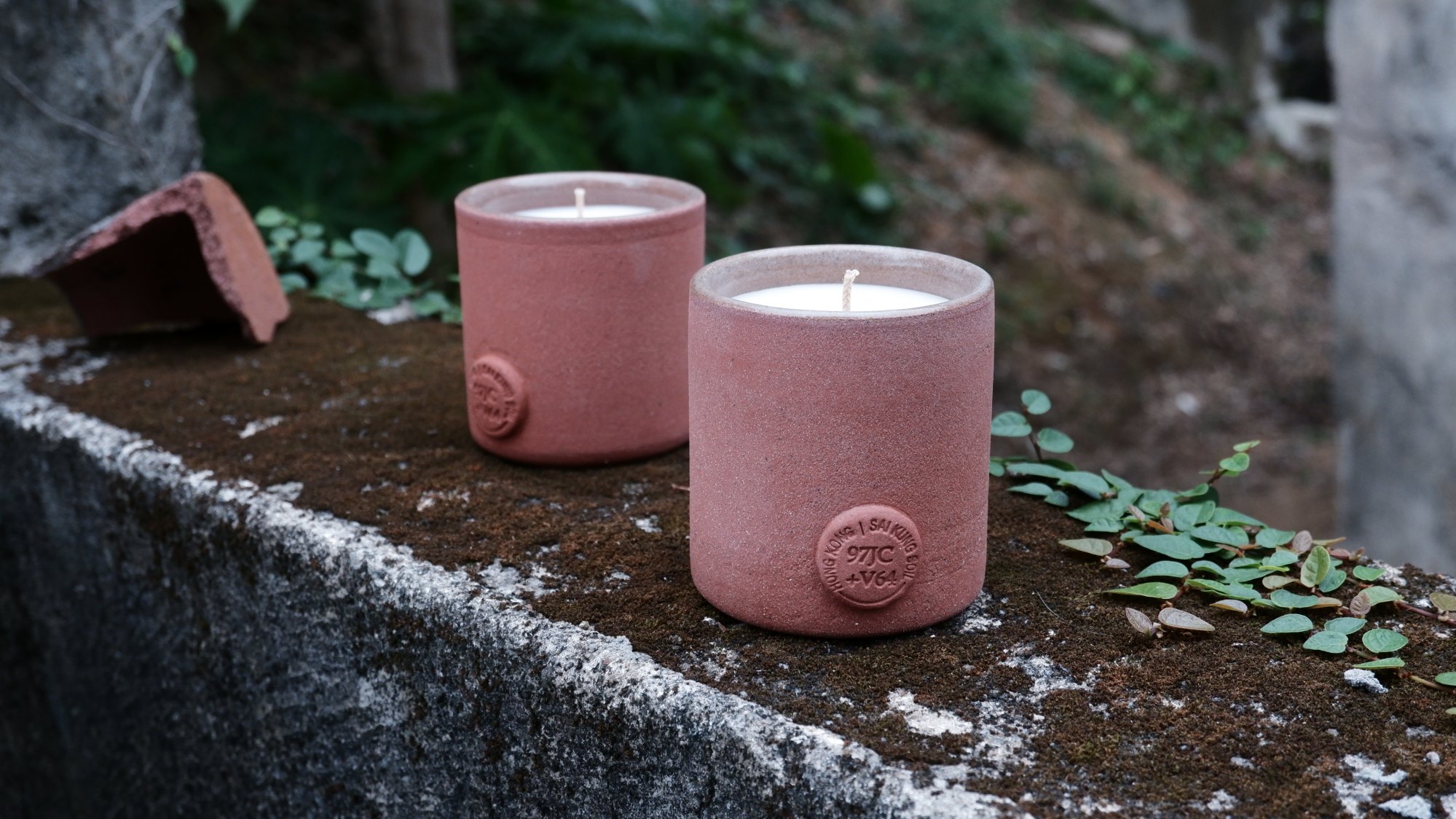
While the market seems ready for locally sourced and produced ceramic homewares, Leung would like to see the wider adoption of rammed earth in Hong Kong for building small structures such as village houses.
“In the past, farmers would routinely build their own houses with rammed earth,” she says. “Today, a lot of designers and architects would love to use rammed earth because of its low embodied energy, ability to regulate humidity, and high thermal mass.
“And in the modern context, when we are so reliant on imports, the proximity of the material sourced in construction is important.
“It’s also a reminder to source mindfully and treat our land with care and respect: I very much see the future economic and cultural significance earth could bring.”
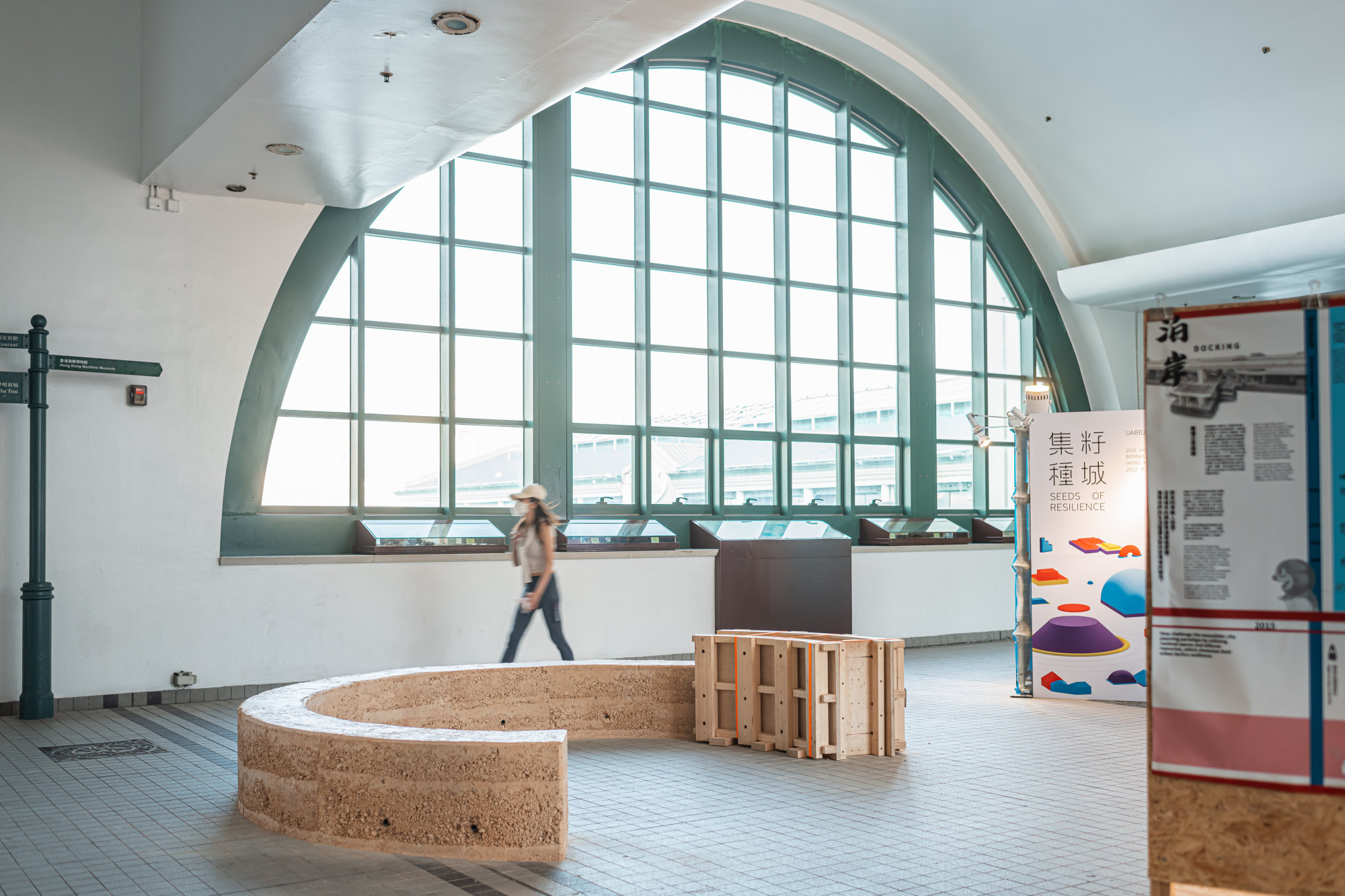
“The students pick any type of waste or leftover material they think might have potential, imagine an end product, and then do a lot of experiments, formula testing and mock-ups to gauge its viability,” Cheung explains.
The aim, he says, is “more about investigation” than product commercialisation. “I’ve been trying to push the boundaries with them,” he adds of the course, Alternative Material, launched in 2021 and continuing in 2023.
It is up to the students to pursue the work privately, should they choose to.
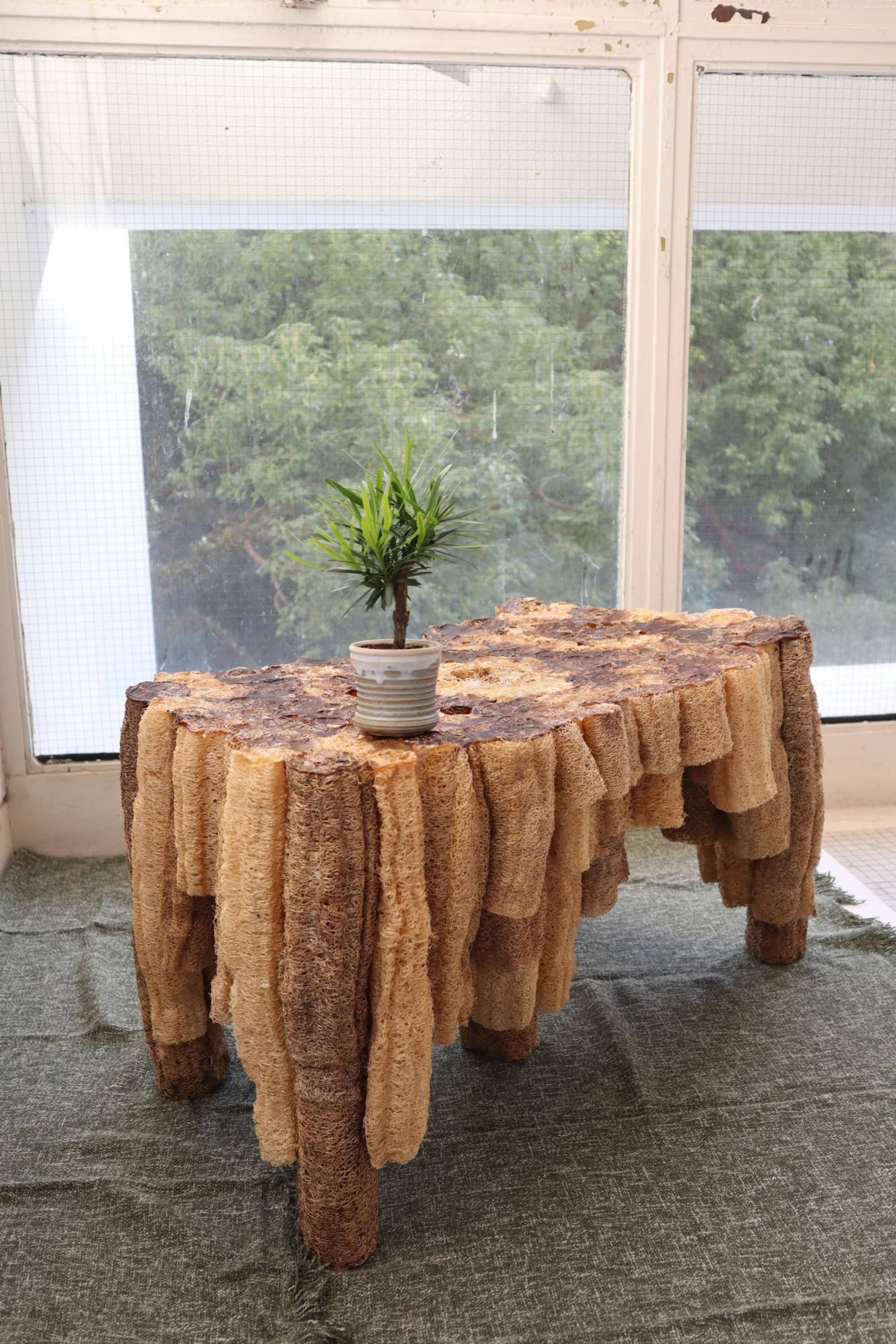
Students Winnie Heung Tsz-kwan and Nomy Yu Jianing led a project experimenting with loofah, a plant used as a natural sponge for scrubbing and cleaning. Their aim in exploring its potential for furniture production was to use a resource grown in abundance in rural China, while having a social impact as well.
“As architecture students, we are sensitive to the beautiful structure of the loofah,” Yu says. “It’s also very cheap,” adds Heung.
Using natural binders such as glycerine and coffee grounds, the group manually made two prototypes – a coffee table and a lampshade. During a pop-up display at PMQ in Hong Kong’s Central district early last year, the group also held a how-to workshop.
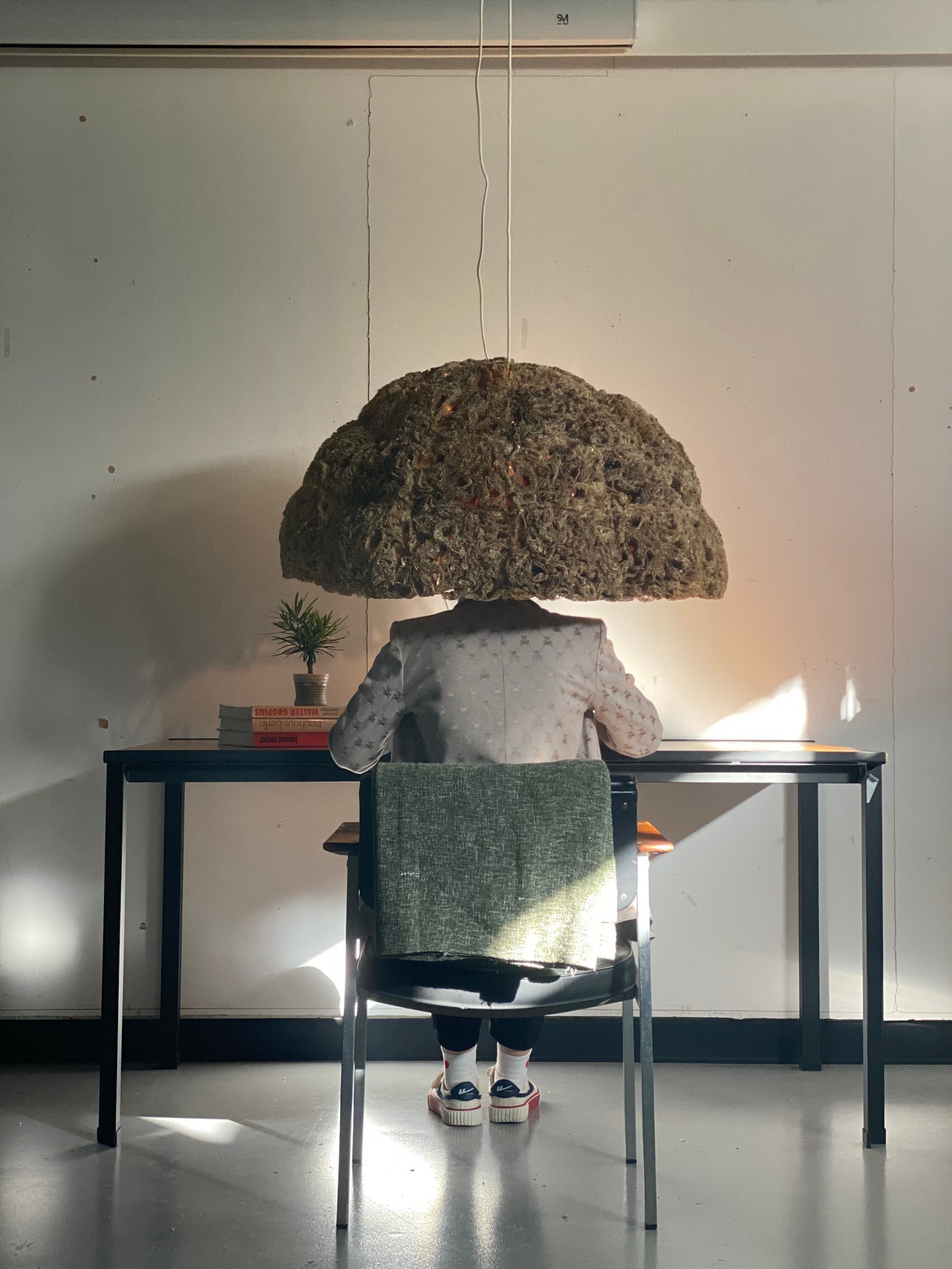
Yu and Heung say they would like to see these 100 per cent biodegradable pieces go into commercial production. They also hope to produce a DIY kit farmers could use to make furniture for sale, thereby boosting their income.
Another project explored the potential of egg and oyster shells as a sustainable construction material.
By adding oyster shells to the mix, the students came up with a formula showing that these calcium-rich bivalve shells, when pulverised, baked in an oven and soaked with a fabric mesh reinforcer, can be as strong as cement, only far more eco-friendly.
One “really good exploration with a surprising outcome” came after students gathered hard and soft crustacean shells from local seafood restaurants.
“They eventually found out that, when heated in an oven to a certain degree, the chitosan, shell powder and bone glue mixture would rise like a dough, becoming a much larger object with air enclosed inside,” Cheung says.
Though early in the experimental stage, the students’ work suggests potential for a lightweight, organic building material with inbuilt insulation.
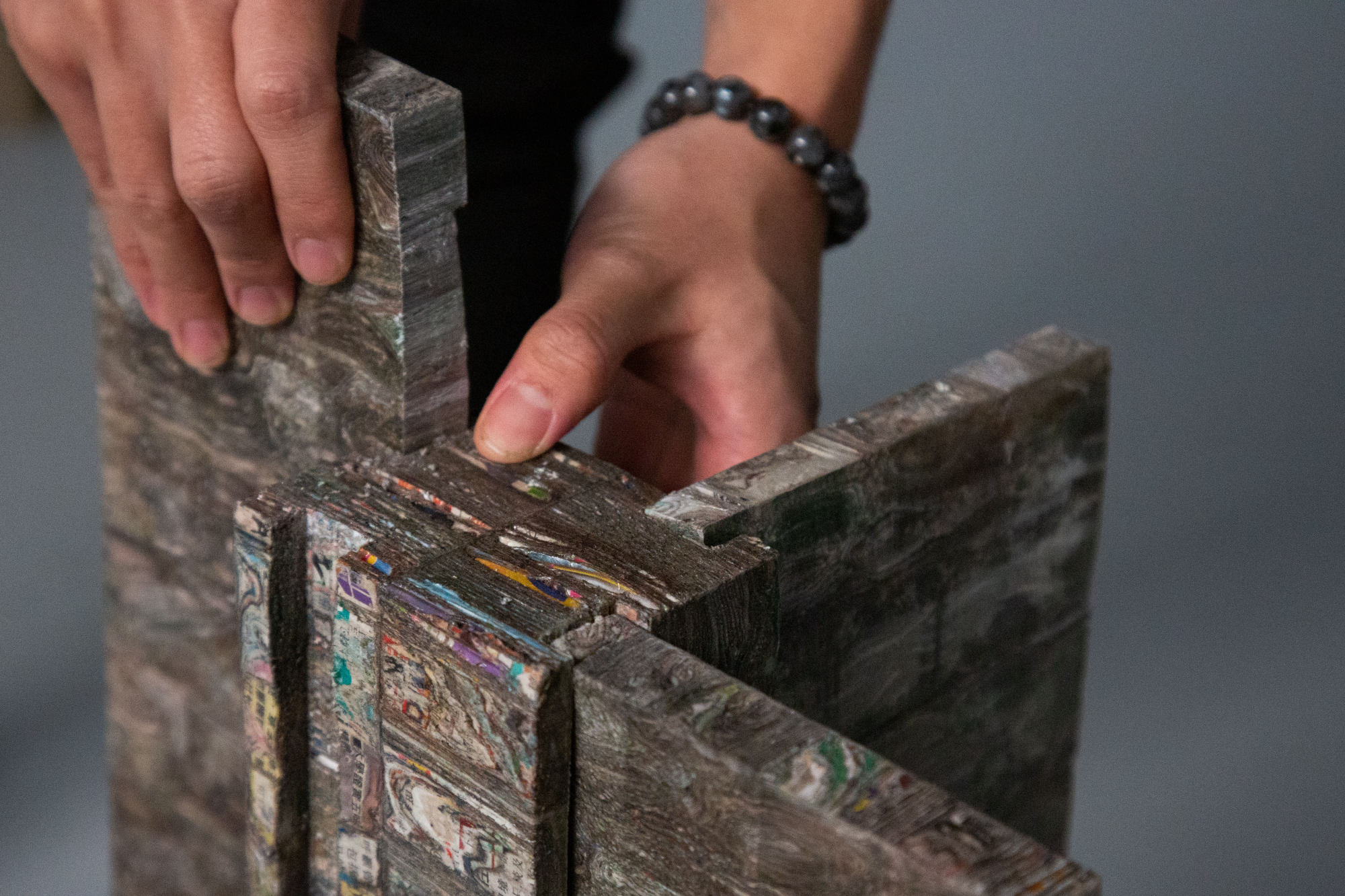
By experimenting with paper reuse, one group aimed to reduce the amount of waste dumped in landfills; paper products are the third-largest component of municipal waste in Hong Kong.
They found that when paper pulp is mixed with xanthan, an emulsifier used for thickening food, then compressed until it solidifies, a structural mass is formed.
This material could be cast into blocks, or 3D-printed via a robotic arm if sand is added. They also developed another material from rolled-up paper that can be cut into slabs to form the top of a stool with a woodgrain appearance.
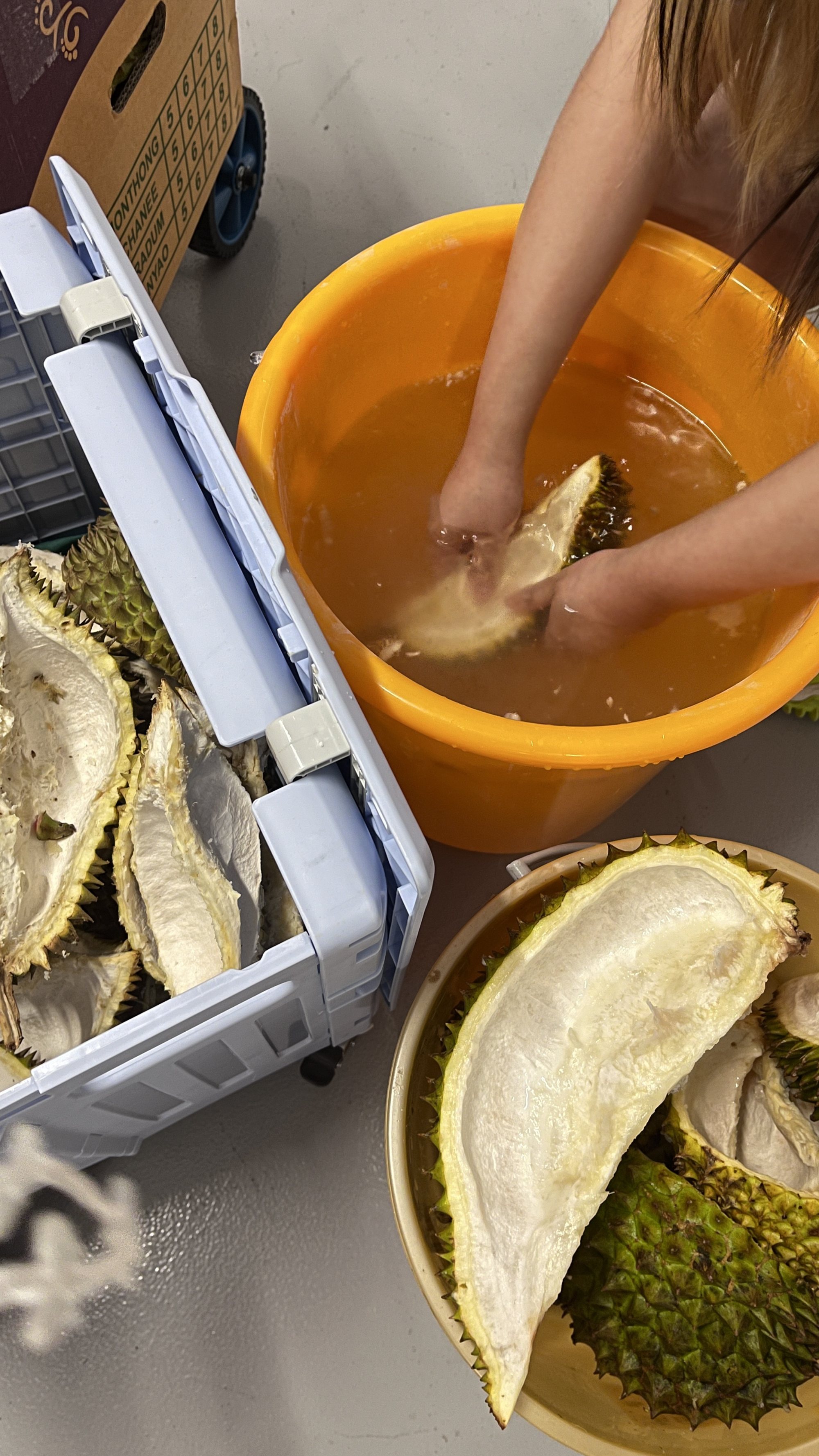
“Although we have successfully created a material that is 3D printable and significantly hardens when dried (almost rocklike), we are looking further into optimising the drying process as well as further testing to validate potential in construction applications,” he said.
The group is now looking into larger-scale production “because we have received a lot of interest in that stool and material, specifically for furniture applications”.
Sabrina Siu Man-yan and Angelique Nicole worked with durian – a fruit whose skin, once the fibre is extracted, can be compressed into a bricklike block.
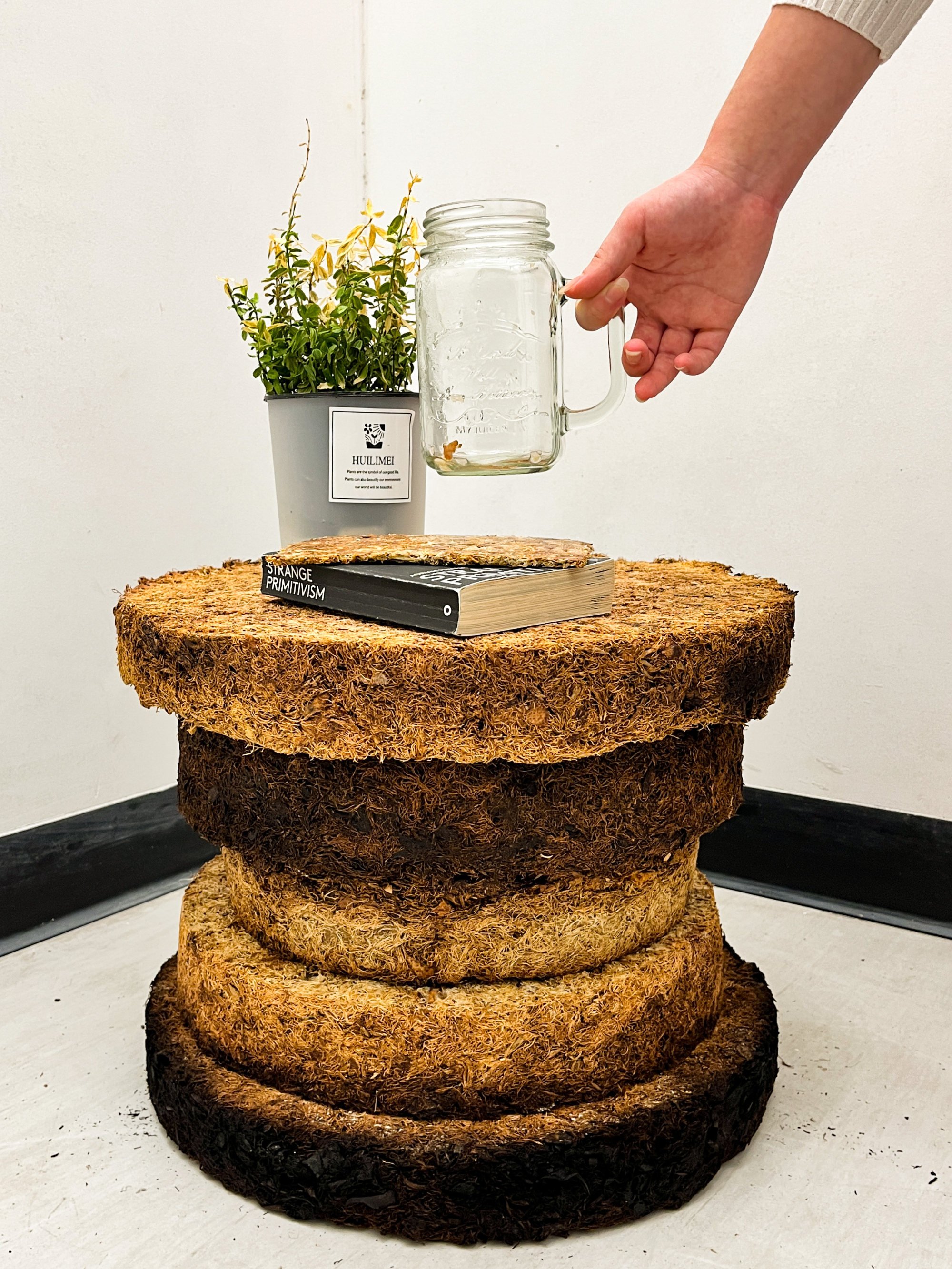
Similar to hempcrete, a biocomposite made from the inner core of the hemp plant, durian skin could be another truly sustainable construction material even if, during its production, the smell is rather off-putting.
Another group used powdered blood, a slaughterhouse by-product.
“Meat is one of the most consumed food types around the world, and yet its biggest by-product (blood), although nutrient-rich, has very limited treatments,” explained Gabriella Chau, one of the project leaders. “We wanted to tackle the problem of blood waste in slaughterhouses.”
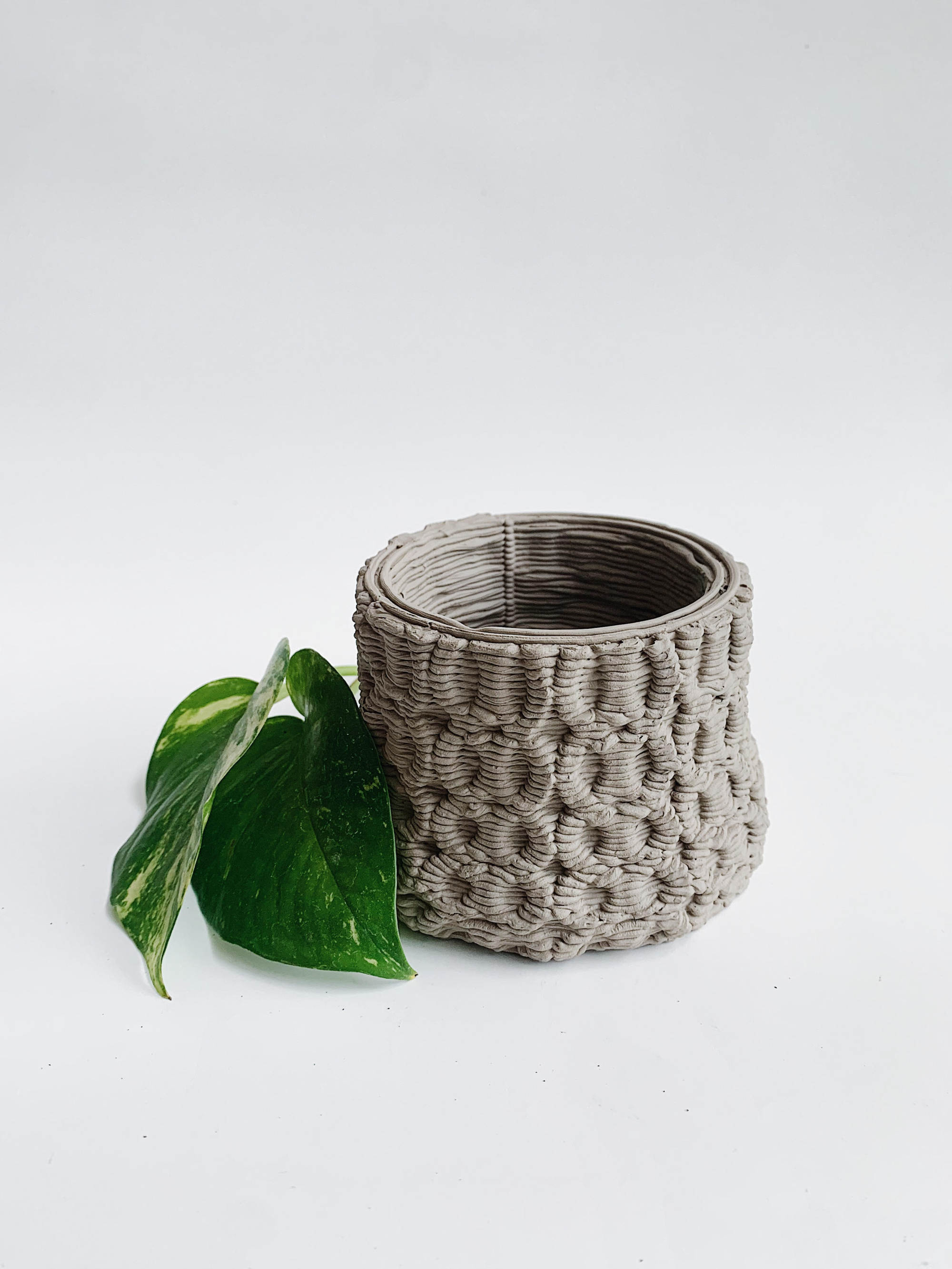
The group’s idea was to incorporate blood powder into a self-watering planter programmed to release nutrients into the soil slowly. Employing a form designed using parametric software, the product was realised in 3D-printed clay.
Chau says the team sees many opportunities for this material beyond household objects. “With the right tools and techniques, we see our concept being applied to urban landscape planning and even in the architecture field,” she said.
Cheung says such experimentation is “urgent” given the impact of climate change and overconsumption in general.
“I try to push designers to work out materials that will respond creatively to this situation. It’s actually alarming and urgent,” he says.
Cheung hopes that, eventually, the course he is teaching at HKU will build transferable skills for the continuing education of designers.
Without the ability to appreciate natural resources, and to think and act sustainably, “I would say designers are contributing to even more waste in the world”, he says.
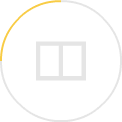