How 3D printing is changing Swiss luxury watchmaking
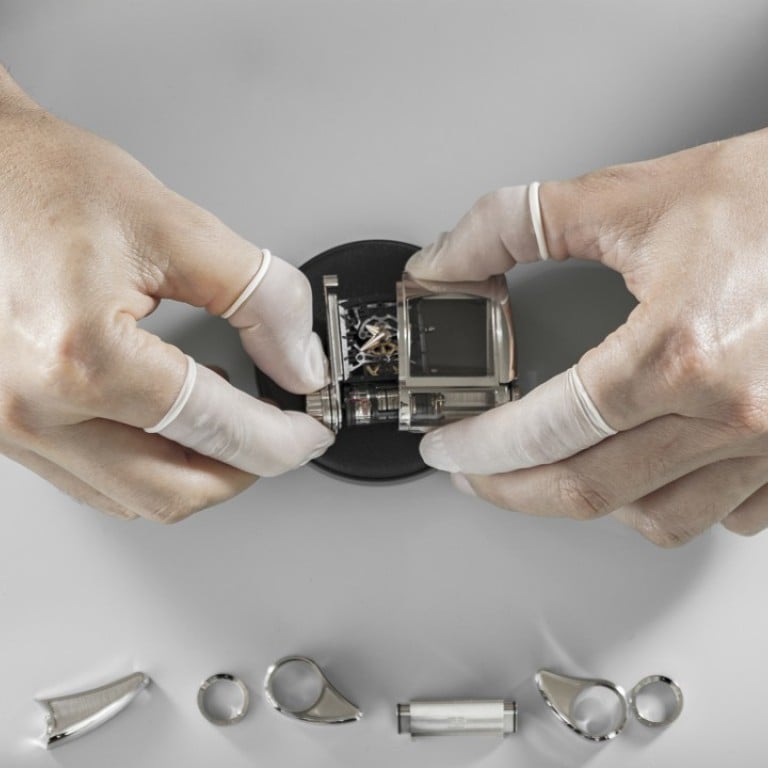
A number of luxury watchmakers are embracing 3D printing and other hi-tech innovations, while others prefer to stick to traditional craftsmanship and techniques
Beating inside the mechanical heart of the Parmigiani Bugatti Type 370 prototype are some parts quite unlike the others – parts that, instead of being crafted by milling machines, have been 3D printed.
“We use 3D printers almost on a daily basis,” says Florin Niculescu, Parmigiani’s vice-president of product development. “It’s a great help for us to validate the design as quickly as possible and have something ‘real’ to show designers and watchmakers.”
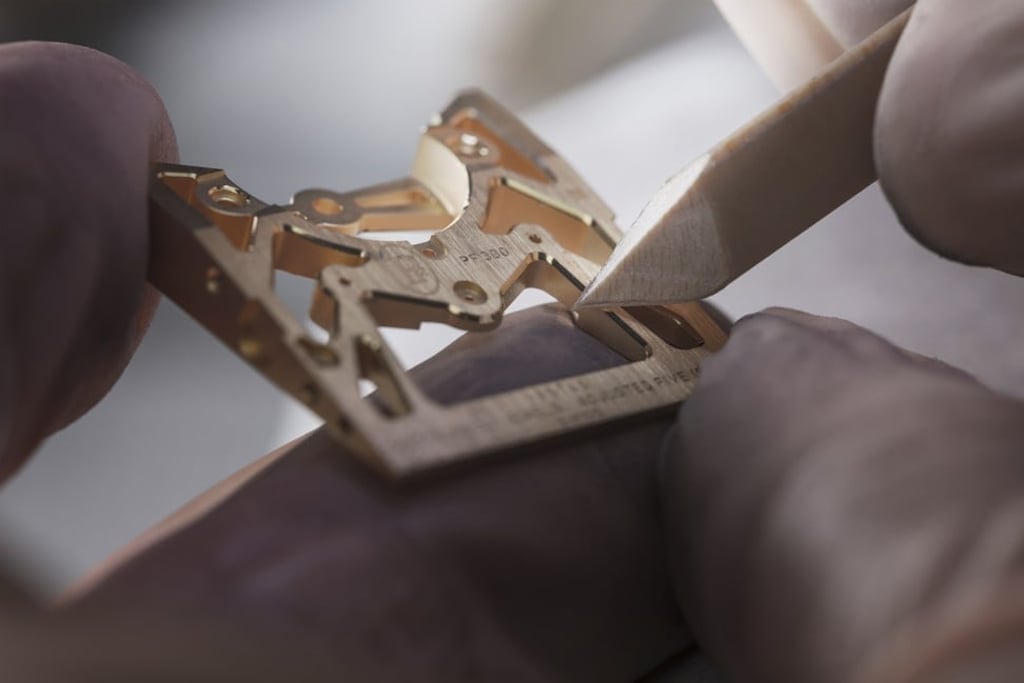
Mechanical watch purists might frown upon the new trend. However, luxury watchmakers are reinvigorating the century-old industry by embracing 3D printing and other hi-tech innovations – in materials and in mechanisms – to improve efficiency and ergonomics and create groundbreaking designs.
3D printing is becoming a common and powerful tool for luxury watchmakers for prototyping. Some are printing specific watchmaking tools which otherwise would take specialised tool makers hours or even days to complete.
“3D printing has allowed us to react much quicker,” says Christian Knoop, IWC’s creative director. “We use the technology to print prototypes and run mechanical simulations which have changed the way we [traditionally] develop products.”
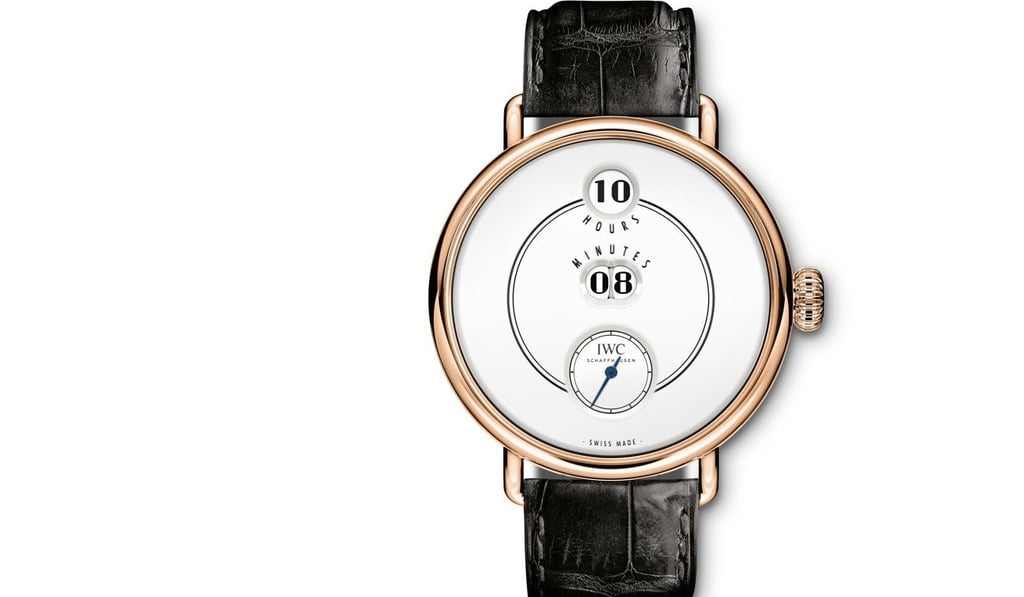
The brand’s CEO, Christoph Grainger-Herr, adds that “speed and control” are the main benefits of incorporating the technology into the R&D process.
“I think this is a wonderful basis for even more high-quality movements, and in terms of movement autonomy and servicing, it makes perfect sense,” Grainger-Herr says.