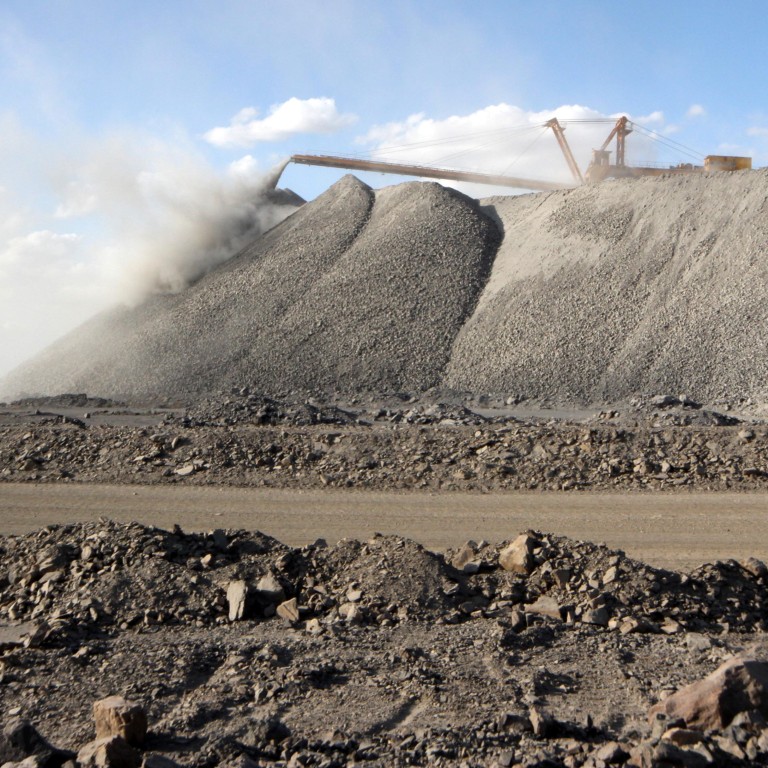
Chinese rare earth tech innovation aims for faster, cleaner extraction: paper
- Guangzhou team says their electric power method could make China even more competitive in global supply chain
- ‘Technique is viable, both environmentally and economically, revealing new paths for the sustainable harvesting of natural resources’: Professor He Hongping
Rare earth elements are essential in various industrial and military applications but mining them is extremely time consuming and the large amount of chemicals required to separate these elements from other materials usually comes at a high environmental cost.
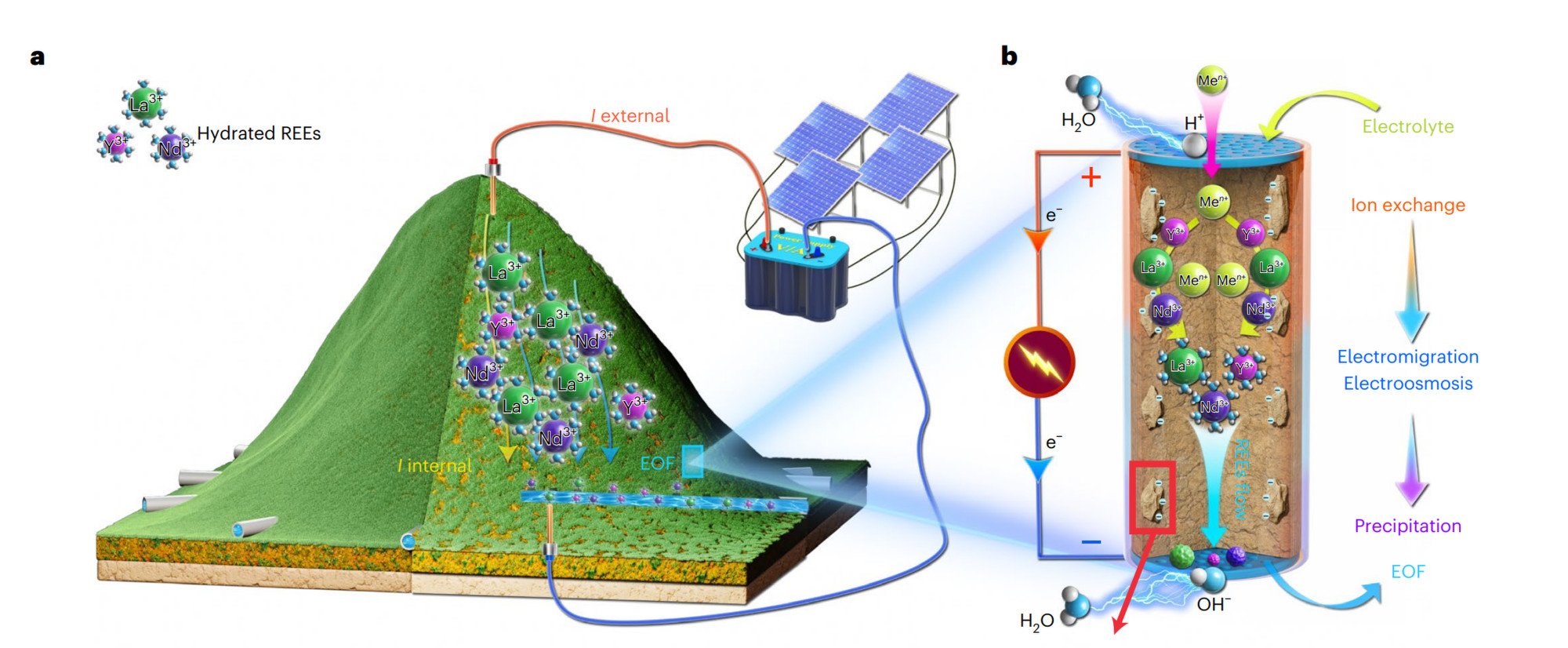
China plays an important role in global rare earth production, especially for elements with higher molecular weight.
“The ion-adsorption deposits in southern China supply more than 95 per cent of the global heavy rare earth elements demand,” said Professor He Hongping, head of the Guangzhou Institute of Geochemistry, Chinese Academy of Sciences, in a paper published in the peer-reviewed journal Nature Sustainability on October 31.
Traditionally, workers use ammonium sulphate as a leaching agent to extract rare earths from natural deposits, then use ammonium bicarbonate to remove impurities. Finally, they obtain ionic rare earth concentrates by roasting.
Both chemicals are harmful to the environment. Ammonium salts may penetrate into the soil and remove minerals such as calcium and magnesium that are important for plants and the ecosystem. For example, many microorganisms stop being active after chemical immersion. Restoring these minerals can be a difficult and costly process.
To solve this problem, He and his group proposed a green, efficient and selective recovery of rare earths from the Earth’s crust that would require less of the solution to rinse the ores by applying an external electric field to the mining area.
The rare earth ions are activated by the electric current and migrate in a designed direction, making collection more efficient. And with more charged energy, the rare earth ions gather at the cathode and hinder impure metal ions from binding.
To test this unprecedented method, the team conducted a small-scale experiment in the lab, a scaled-up trial and further on-site field experiments in Guangzhou.
In the scaled-up test, the recovery rate for rare earth elements using their new method was reported to reach 96 per cent in 67 hours, while the recovery rate using the traditional leaching method was only 60 per cent in 130 hours, the team said.
In the field experiment, they reported the recovery rate when using their method reached more than 90 per cent in 11 days, and the amount of leaching agent used was reduced by about 80 per cent compared with the traditional ammonium method.
The team said the electricity consumption could be provided by photovoltaic panels, which might further lower the production cost.
“The annual cost for conventional leaching is 2.8 times higher than the new method,” He wrote in the paper.
“The technique is viable, both environmentally and economically, revealing new paths for the sustainable harvesting of natural resources.”
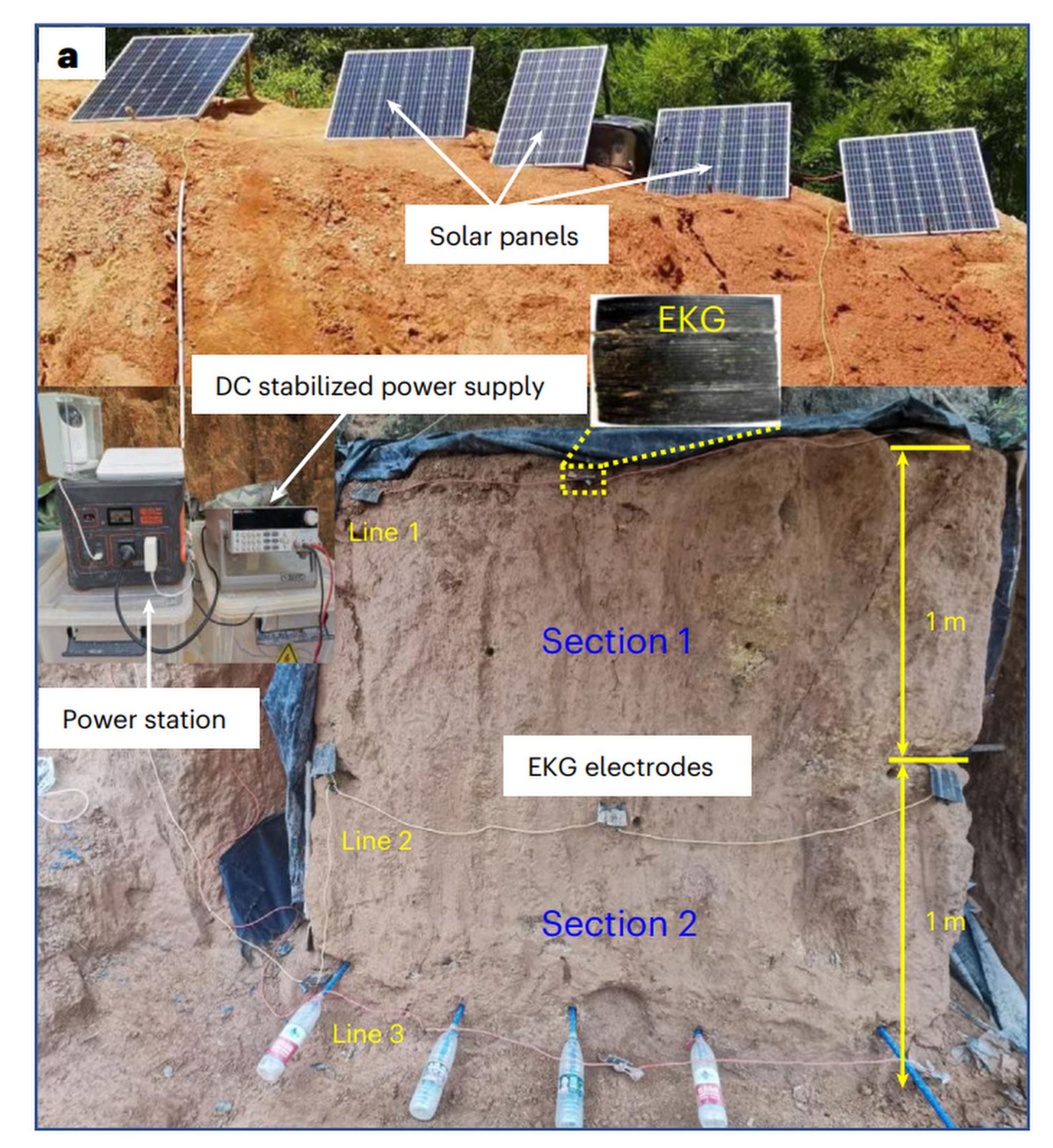
He’s team declined the South China Morning Post’s interview request because of the sensitivity of the technology.
While China produced 70 per cent of the world’s rare earth magnetic materials, Chinese production companies often did not know the end user of these high-value minerals, said Li Wei, an academician with the Chinese Academy of Engineering, was quoted as saying in report by state news agency Xinhua in October 2020.
“It takes 920 pounds [417kg] of rare earth materials to make an F-35 combat aircraft, 5,200 pounds to build an Arleigh Burke DDG-51 destroyer, 9,200 pounds to build an SSN-774 Virginia-class submarine,” according to a report by the Congressional Research Service, a public policy research institute of the US Congress.
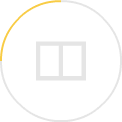