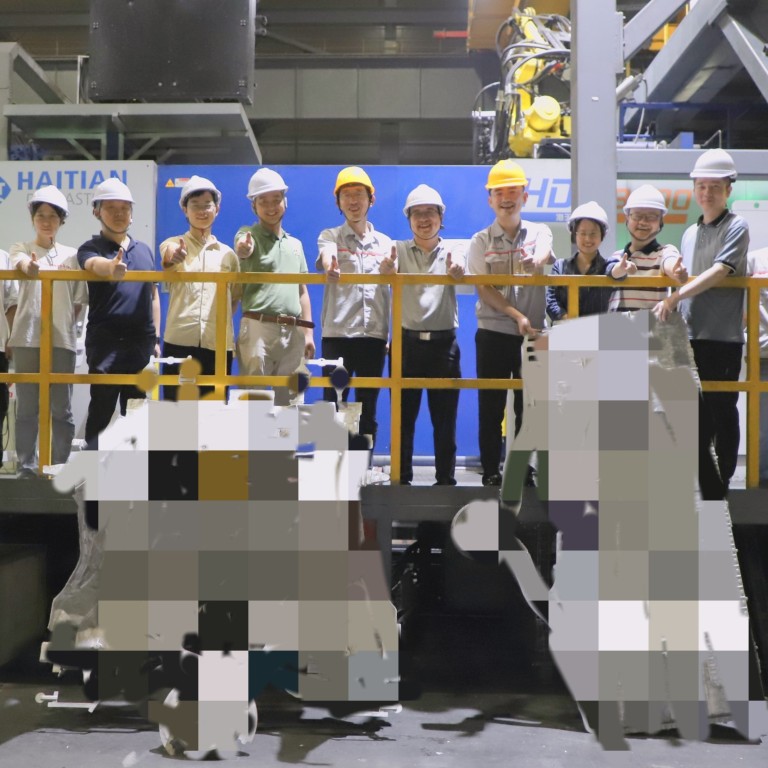
Chinese scientists say supersized magnesium parts pave the way for cheaper, lighter cars
- Researchers in China produce giant car parts using technology similar to Tesla’s ‘gigacasting’ – a process that has cut production times and costs
- Magnesium alloys could absorb impacts and offer advantages over more common aluminium-based materials, professor says
Researchers in China say they have developed supersized magnesium alloy auto parts that could significantly reduce the cost of making cars and promote lightweight vehicle designs.
The scientists produced the two giant parts – a car body and a battery box cover – from a single mould in one casting.
Each part measures over 2.2 square metres (23.7 sq ft) – the first of their size to be made from magnesium alloy, according to a news release from the National Engineering Research Centre for Magnesium Alloys (CCMg) at Chongqing University on June 27.
China curbs critical metal exports in retaliation for chip-related sanctions
CCMg worked with Chongqing Millison Technologies Inc and Boao Magnesium Aluminium Manufacturing Co Ltd to produce the two pieces.
Chongqing Millison Technologies provided the die casting system used for processing, while Boao Aluminium Manufacturing has experience in developing magnesium alloy dashboard and seat frames.
Compared to traditional casting, high-pressure “mega casting” offers advantages such as smoother surfaces, stable dimensions and the ability to mould in a single casting.
The technology has sped up Tesla’s production in its Shanghai and Berlin factories.
Thanks to gigacasting, the Tesla Model Y’s rear underbody is now made of two large pieces of cast metal compared to the 70 parts used in a previous iteration of the car, while the number of welding points was reduced from over 700 to 50 and the production cycle was shortened from 1-2 hours to 3-5 minutes.
“Fewer parts, lower costs and a simplified production line have contributed to Tesla’s industry-leading profitability. The weight of the rear body was reduced by 30 per cent, and manufacturing costs could be reduced by 40 per cent,” Reuters said in a June report about gigacasting.
Jiang said replacing commonly used aluminium alloys with magnesium alloy offered even more advantages when used with high-pressure casting. Magnesium is lightweight and abundant, and magnesium alloys can absorb vibrations and dissipate energy, he said.
While there are challenges to creating large magnesium alloy castings, such as filling the models with molten alloys and defect control in narrow spaces, the researchers said they had overcome them through structural design, raw material purification, casting process optimisation and other means.
China’s EV sales back on track as better cockpit tech lures young drivers
Magnesium alloy castings are similar to aluminium alloys in terms of life expectancy and production costs.
“Despite magnesium alloys’ slightly higher material cost compared to aluminium, the faster production speed and ability to produce more parts from the same amount of material makes the overall cost per part comparable,” Jiang said.
Images of the two huge car parts have been blurred out on Chongqing Millison Technologies’ website, and it is not clear how the parts will be used. The company declined an interview request.
Industry insiders said the trial casting would advance the large-scale use of magnesium alloys in large complex structures.
“It holds strategic significance for the lightweight construction of cars,” the Chongqing Daily said in a report.
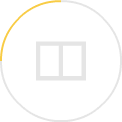