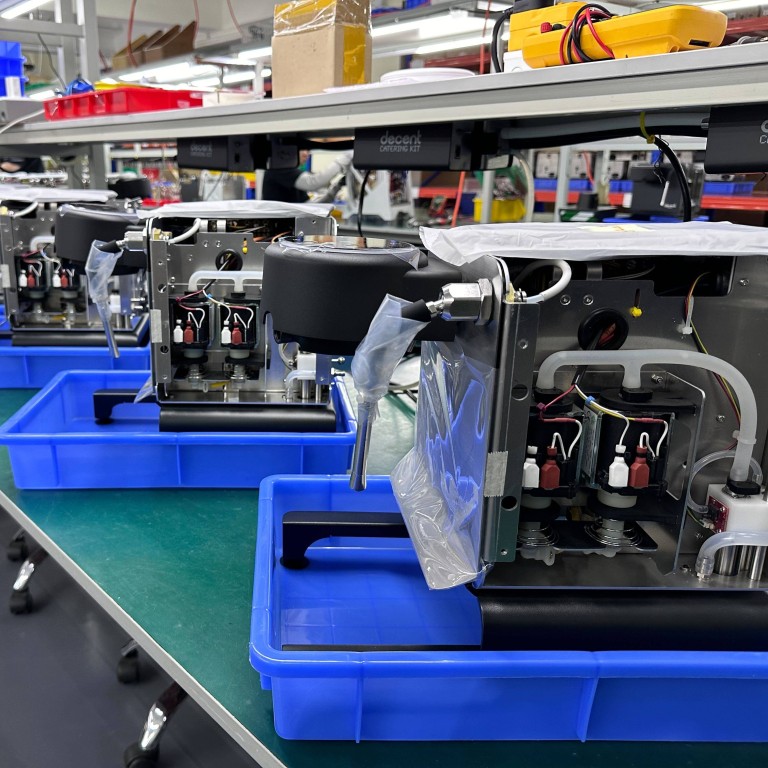
Hong Kong-made espresso machines? ‘Boutique’ manufacturers tap tech for efficiency, target government funds for ‘smart’ shake-up
- Companies that use more tech to switch to ‘smart’ production lines can get help from HK$10 billion scheme
- Three Hong Kong companies say tech has made a difference to the way they work or the products they sell
Tang Wing-sze had plastic covers over her shoes as she entered her Hong Kong factory’s “clean room” to check on freshly assembled electronic components on circuit boards.
But the founding member and marketing director of PDSTE was quick to point out that the 500 square metre unit in Fo Tan, in Sha Tin district, did much more.
Established in 2017, the firm has 30 employees working on everything from product research and development (R&D) to making electronic parts for coffee machines, smart devices that alert family members if an elderly person has a fall, and more.
The diverse nature of the work was reflected in the company’s unusual name, Tang said.
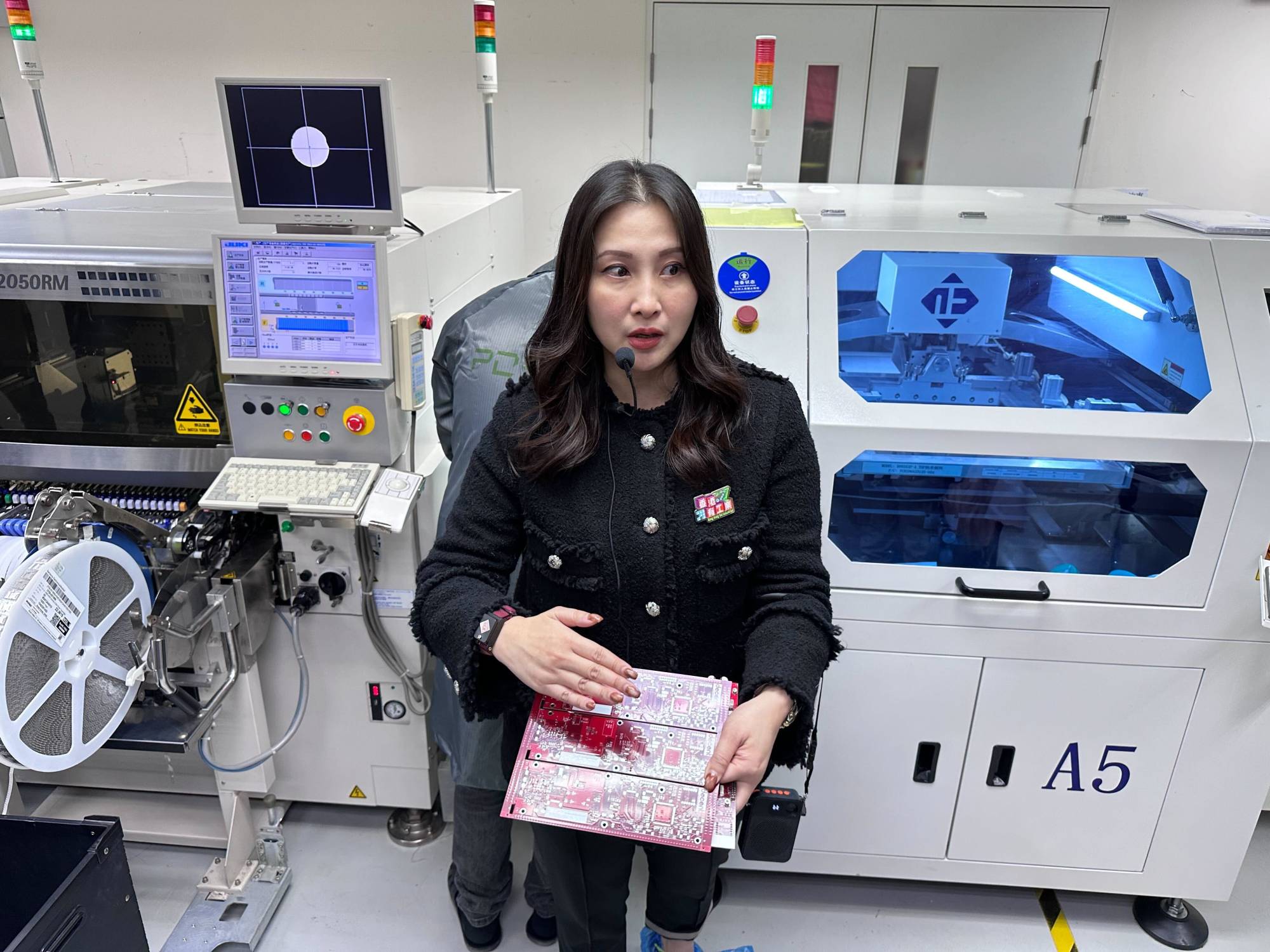
“We are kind of greedy and want to position ourselves as a Hong Kong boutique factory which provides Product, Design, Services, Technology and Engineering support,” she said. “No Chinese words can embody our vision, so we just named our business PDSTE based on the initials of those elements.”
To cater to an evolving consumer market which demands frequent design changes and smaller quantities of multiple variations of the same product, the company planned to invest HK$6 million (US$767,740) in a smart production line that would improve productivity by 1.5 times.
Similar to a growing number of local manufacturers, the company is looking at ways to up its game by using technology to streamline labour-intensive production tasks, achieve sustainability and maintain its competitive edge.
City leader John Lee Ka-chiu announced in his policy address last October that a HK$10 billion industrialisation acceleration scheme would be set up to help companies use more technologically advanced manufacturing methods.
Through the Re-industrialisation Funding Scheme, the government would provide subsidies to cover half the cost of establishing smart production lines, with the aim of growing the number of such facilities from 30 in 2022 to more than 130 by 2027.
PDSTE is among the companies hoping to get government support for their plans.
“The smart production line will be a game changer for us,” Tang said. “By being able to simultaneously assemble multiple electronic components onto circuit boards at a single station, the manufacturing process will be significantly sped up.”
Integrating artificial intelligence into the process enabled real-time data tracking, eliminating the need for staff to do the job manually and saving time.
Although it cost more to run a production line in Hong Kong, Tang said the growing start-up scene provided companies such as hers “the best opportunities to thrive”.
Tang recalled that her first project involved a biologist wanting a machine to analyse the DNA of fish, as a prototype based on his idea did not work. Her team produced two machines that did the job, after months of discussion and R&D efforts.
“I don’t know whether those machines were commercialised in the end, but we can serve as a platform for individual innovators and start-up owners who are stuck at the idea stage and don’t have the resources for mass production and commercialisation,” she said.
“That’s our edge in Hong Kong. Factories elsewhere may charge less for a product, but we offer customised service catering to our clients’ pain points.”
Decent Espresso, a coffee machine manufacturer established in 2015 which uses PDSTE circuit boards, chose Hong Kong as a base because of the city’s international status and sophisticated logistics industry.
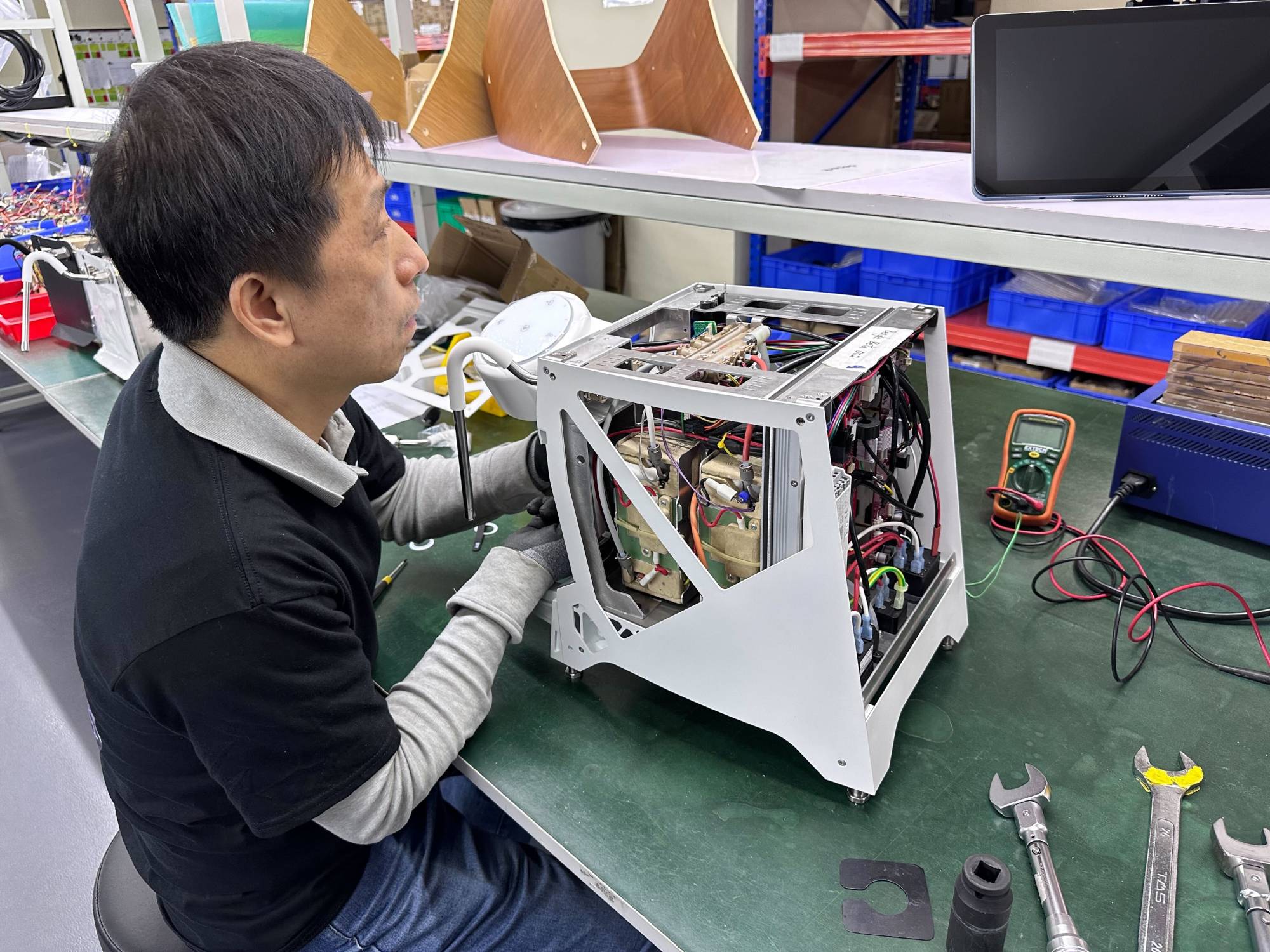
CEO John Buckman met Tang at a trade show years ago, when his company was selling only a few coffee machines a month.
With machines known for precision, customisable settings and advanced brewing technology, the brand has gained a reputation for quality and innovation.
“Not only does it look like a computer that makes coffee, it is a computer that makes coffee,” Buckman said. “Because it’s software based, it evolves.”
The company has sold more than 10,000 units across more than 40 countries worldwide.
The firm’s operations manager, Nicole Chow Tsz-wing, said: “In Hong Kong, favourable tax regulations and strong government support for high-end production like ours allow us to enjoy a high degree of freedom in technological development.”
While its main market has been in Europe and America, the company has made inroads in Southeast Asia where she said there had been “a surge in coffee culture” over the past three years.
“Having our base in Hong Kong has been instrumental in enabling us to effectively promote our products in the region,” she said.
Meanwhile, at the Tuen Mun landfill, the city’s first and only steel-rolling mill is also making plans to have a smart production line by next year to tap into growing demand for green initiatives in the city and the Greater Bay Area.
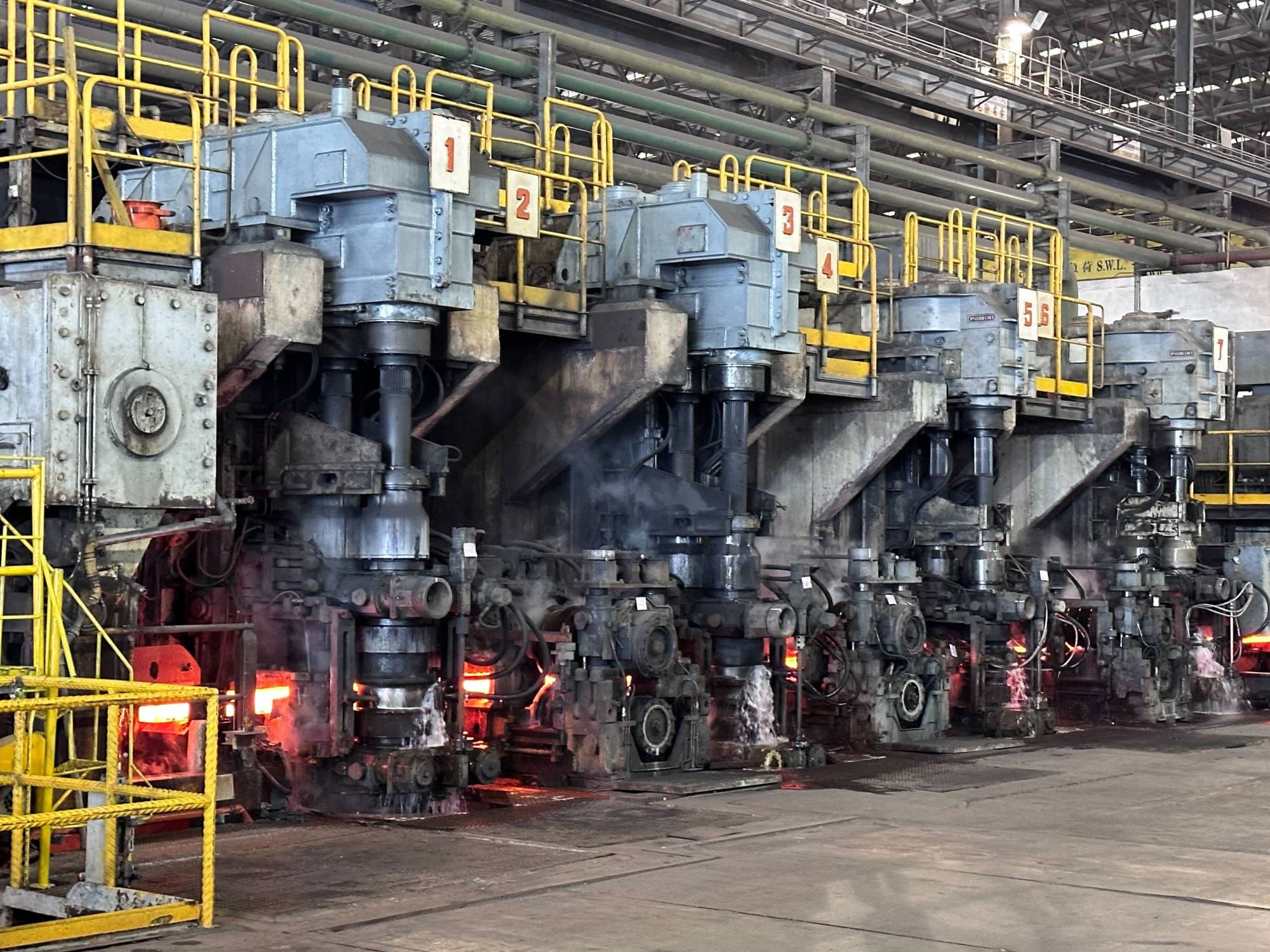
Samanta Pong Sum-yee, a director and third-generation leader of 68-year-old family business Shiu Wing Steel, said diversification beyond local construction was urgently needed as firms vied to make the most of opportunities in the bay area, made up of Hong Kong, Macau and nine Guangdong cities.
“A new production line will enable us to have the technology and capability to meet the region’s standards and expand our market to the bay area,” she said.
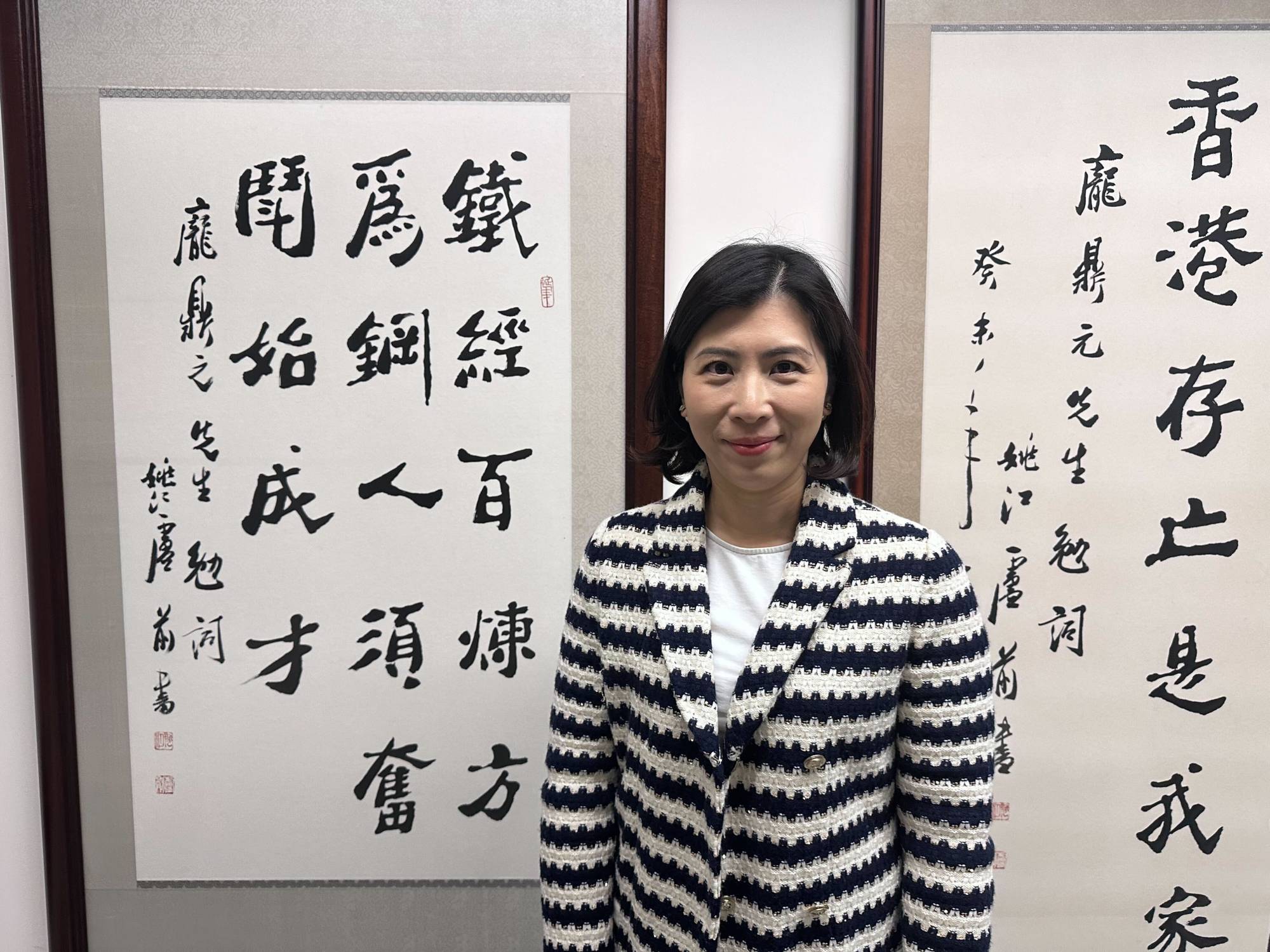
The Hong Kong Productivity Council is the steelmaker’s consultant in its move to a smart production line.
In 2022, Shiu Wing Steel applied for funding from the Innovation and Technology Commission, which provides a 40 per cent cash rebate for a company’s spending on recognised R&D projects.
The latest data showed that as of 2022, the commission had approved 17,946 projects with a funding of HK$6.23 billion.
Pong said the company also planned to build electric-arc furnaces next year to produce recycled steel, which emitted less carbon compared with conventional blast furnaces.
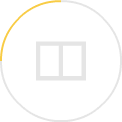