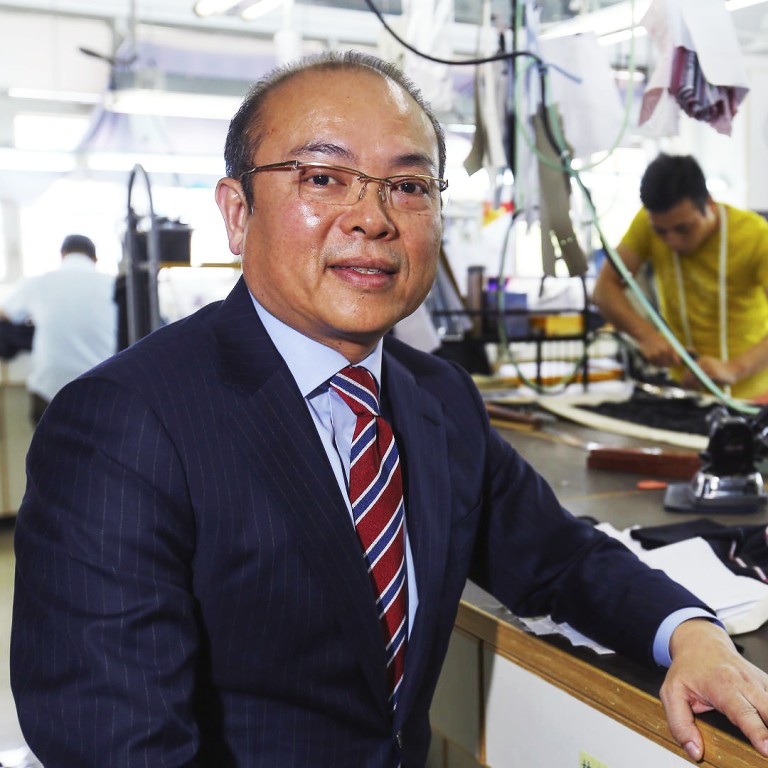
The manufacturers moving production from China back to Hong Kong
Rising labour costs over the border are sparking a mini reindustrialisation of the city
Alan Cheung Yick-lun may just be part of a brave new world for Hong Kong industry. Local manufacturing had long been hollowed out by the shift to low-cost bases in southern China, but factories are starting to come to life again here, due to entrepreneurs such as Cheung.
He recently opened an 80,000 sq ft facility in Tsuen Wan, where his Grandion garment company makes T-shirts primarily for online retailers. Although Grandion operates three factories employing more than 3,000 workers in China, the new facility is the company's first in Hong Kong.
The appreciating yuan and rising labour costs have led to an exodus of manufacturing from the Pearl River Delta. But while some industrialists have relocated to low-wage countries such as Myanmar, others have set up in Hong Kong.
Federation of Hong Kong Industries chairman Stanley Lau Chin-ho sees a nascent revival of small-scale manufacturing in the city.
"We encourage businessmen engaging in innovative, high-value-added manufacturing to come back. These are not the labour-intensive industries, but those that involve hi-tech equipment such as health care, watches and jewellery. The entire process, from research and development to design and production, can be moved to Hong Kong."

Federation statistics show the number of Hong Kong companies with factories in the Pearl Delta region has dropped from 55,000 in 2006 to 32,000 in 2015.
Grandion's new Tsuen Wan facility, which employs 100 workers and designers, is a response to the changing business environment, says Cheung, its managing director.
Set up in 1996, Grandion makes garments for clothing chains from IT to Zara and at its peak employed about 6,000 workers in China. But as salaries rose in response to a central government bid to drive domestic demand, the company increased automation to reduce reliance on labour and to retain clients by offering value-added services.
"In the past, we got orders and designs from clients. Our job was only to source the fabric and make the clothes. Now, we also design for clients," Cheung says, citing Zara as an example. "Our clients are willing to pay for this extra service."
Now he aims to tap a new market serving the ranks of online retailers popping up across the world.
"Whether you make one T-shirt or 100, the process is the same. But with a digital printer, we can shorten the [production] time from one week to one minute. It's especially good for orders from online stores which cannot afford to keep a large inventory," he explains.
At the same time, Cheung has carved out part of his Tsuen Wan facility as an incubation centre for fashion entrepreneurs. "We want to help local design graduates who cannot afford to put their creations into production. We want to become like the Dongdaemun district in Seoul, where designers, manufacturers and retailers gather together."
For the Defond Group, an established maker of switches and electrical components, Hong Kong offers the flexibility and speed that is needed for a globalised business.
The company has production bases in Hong Kong, Italy and China, but opened a new 3,000 sq ft facility next to its Chai Wan factory to undertake additional services such as testing and special finishing for its clients, says Martha Hao Mui-fung, who heads its electromechanical modules division.
"Some clients put a lot of emphasis on protecting intellectual property. They are worried that their designs might be leaked if production is done [in China]," she says.
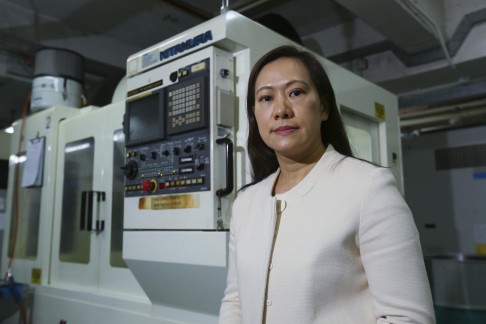
As a result, they have had to recruit more staff and install new machinery such as 3D printers at their Hong Kong factory.
The market is no longer dominated by multinationals as more people buy things on Amazon or Taobao, Hao says, and these products are often created by start-ups, which form a growing number of Defond clients.
One example is a US start-up that designed high-visibility motorcycle gloves that light up when the wearer touches thumb to forefinger.
"Our [Chinese] factory makes the electrical [circuit] boards, but Hong Kong sews the gloves," Hao says. "For clients like these, whose products have just been launched, their designs are not ready for mass production. New designs may need refinement before being finalised. They only need small quantities. So we do the manufacturing in Hong Kong, where we have tooling machines and 3D printers. And the turnaround time is much faster."
We encourage businessmen engaging in innovative, high-value added manufacturing to come back
Hao believes this mode of production will become a trend of the future, and the company is looking to invest in start-ups that it works with.
Although on a smaller scale, luxury menswear maker Tai Pan Row has also bolstered its workshop in Hong Kong. Peter Lam Kwan-kwong moved production to Guangdong in the late 1980s because of problems hiring young tailors locally. But in recent years skilled tailors have been increasingly hard to recruit in China, too.
"Many migrant workers now prefer to return to their hometowns, which offer more job opportunities as they become more affluent. Over the past decade our [China] staff has halved to 50 people while we increased the number of people in Hong Kong from 10 to 30," Lam says.
"Local tailors are more experienced than our tailors [in China], who are quite young."
Tai Pan Row suits, which retail between HK$10,000 and HK$200,000, are sold in its shops in Central at IFC mall and The Galleria. The garments are hand-sewn by its tailors in a 20,000 sq ft workshop above its administrative offices in Fo Tan.
Its most expensive suits typically require several fittings with clients, which means it is easier logistically if the various processes are completed in Hong Kong. That's why the Fo Tan workshop now specialises in high-end suits.
Allen Ma Kam-sing, chief executive of the Hong Kong Science and Technology Parks, sees innovation and technology-driven reindustrialisation as a way to diversify Hong Kong's economy.
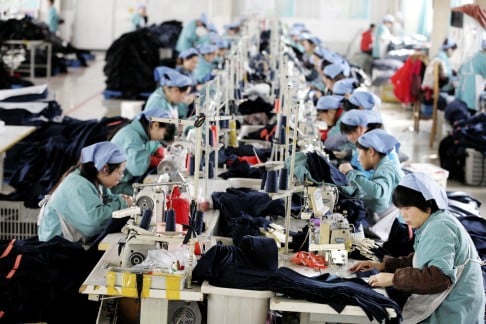
"For the past 10 years, the finance and services sectors have accounted for more than 50 per cent of the gross domestic product, which is not a healthy proportion," Ma says. "Instead of labour-intensive assembly lines, reindustrialisation through innovation and technology can be a way out.
"This can be achieved by introducing new industries in areas such as robotic medical devices, nano materials and precision engineering. Hong Kong possesses important factors such as a sound legal system and intellectual property protection that allow it to become be a fertile hub for research and development."
Still, high rents remain the major hindrance to rejuvenating Hong Kong industry, says Defond's Hao.
"The science park is an incubator for new companies. It does not accommodate large-scale manufacturing involving big machines. An industrialist making, say, medical health care products, has to invest several million dollars upfront to build the infrastructure such as a dust-free automated assembly line. If the landlord were to raise the rent substantially the following year, what would he do with all the installation?"
However, government planners aim to utilise vacant sites at its industrial parks in Yuen Long, Tseung Kwan O and Tai Po to construct factory buildings to house non-polluting, high-value industries.
In the nearer term, Felix Chung Kwok-pan, the legislator for the textiles and garment functional constituency, says an estimated 20 garment makers also plan to move production from Guangdong back to Hong Kong.
"These are mostly high-end producers of mink, fur and leatherwear, which are not labour-intensive industries," Chung says.
They will tap into a HK$500 million proposal for the government to revitalise factories in Kowloon Bay operated by the Clothing Industry Training Authority. The fully equipped factories have been in place for more than 30 years, but are run at far below capacity as they are only used for training.
"We will use government funds to restart the machines, employ workers and help local designers put their creations into production," Chung says, adding that they are in talks with developers to rent to young designers at cheaper rates.
"With fabric suppliers in Sham Shui Po and traders in Lai Chi Kok, the whole supply chain can be linked up like that in Dongdaemun, and more garment makers will return from [China]."
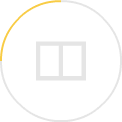