Coronavirus: global textile industry braces for sharp downturn as orders dry up
- No ‘doomsday scenarios’ yet but there are strong signs the world’s textile industry is set for steep downturn due to the economic impact of Covid-19
- Restructuring of the industry could see China become global leader in design and offer a chance to develop new brands, industry insiders say
Chinese fashion marketer Kanvid Studio has managed to weather the worst of the coronavirus so far thanks to some quick adjustments from retail clients who replaced lost shopfront sales with new online business.
But company director Theodore O’Mahony knows his firm’s good fortune is more the exception than the rule.
Clients tell him things will only get worse in the global clothing and textile industry and the crunch will last until the end of next year.
“There was a slight delay in samples reaching us as some suppliers were closed in China. But most are back to work now and we seem to have turned the corner,” he said.
“However, I suspect later in the year the number of styles might be reduced or certainly the volume of [customer] orders … as they look to minimise the risk of overstocking and the associated costs.”
While there are no “doomsday scenarios”, there are strong signs the entire global clothing and textile industry – from manufacturing to advertising and fashion design – is on track for a deep downturn as more retailers dump orders or go under, said Miran Ali, a spokesman for the Sustainable Textile of the East Asian Region (STAR).
The STAR is a network of producer associations promoting sustainability in the textile and garment industry, which includes China – the biggest clothing manufacturer in the world – and producers in Bangladesh, Cambodia, Myanmar, Pakistan and Vietnam.
Even with a pickup in online sales, the industry has not been able to dodge a nearly 50 per cent slump in global clothing demand, Ali said.
The upheaval caused by the Covid-19 pandemic could give rise to a “reshaping” of the industry with some smaller players in China and Southeast Asia disappearing.
Ali said China could solidify its position as the world’s top producer and “reposition” itself by creating its own dominant fashion brands to harness domestic demand, especially when Western retailers were already suffering from the e-commerce revolution.
For now, though, China’s textile industry is still reeling from the pandemic. Export orders plunged in April despite the resumption of almost all Chinese fabric manufacturing operations by the end of March, new data from the China National Textile and Apparel Council trade association showed.
Chinese clothing exports fell US$22.7 billion in the first quarter compared to a year earlier, a drop of 18 per cent, the council said.
Prices of luxury fabrics such as silk have fallen about 30 per cent since the start of the year, while inventories in factories producing silk thread have piled up, according to the council.
The dismal state of the industry was a culmination of a collapse in the clothing supply chain over the past four months, starting with a raw materials bottleneck in China in January due to lockdowns, followed by re-negotiations of payment terms by retailers, and the abrupt cancellation of clothing orders starting in mid-March, according to a report by the Centre for Global Workers’ Rights.
“Some of those orders were entirely finished and ready to be shipped, but the buyers refused to accept order shipments or honour their contractual obligations to pay for these orders,” the report said.
In early April, more than half of the world’s manufacturers were struggling with cancellations of in-process orders.
Primark, the budget fashion chain owned by Associated British Foods, was one of the brands that abandoned its orders in Bangladesh, sparking outrage over its failure to honour commitments to support sustainable and ethical buying.
Major producing countries such as Bangladesh, Cambodia and Vietnam have made pleas for buyers to stand by their contractual obligations, as garment factories in some Southeast Asian nations have closed.
“All parties in the global apparel supply chain are feeling the extreme burden caused by Covid-19,” the Garment Manufacturers Association in Cambodia said in an open letter last month. “However, factories operate on razor-thin margins and have much less ability to shoulder such burdens as compared to our customers.
Gone are the days when Chinese factories made a standard order of 2 million pieces. Now they can make so many different designs and make changes to production quickly
“The consequential burden faced by our workers who still need to put food on the table is enormous and extreme.”
“Gone are the days when Chinese factories made a standard order of 2 million pieces. Now they can make so many different designs and make changes to production quickly,” said Leung, whose company has factories in China, Cambodia and Myanmar.
“These new production units are very lean, they are very robust, and they cope well with changes. Some even have robots and auto hanging systems.
“Because the operations are so reactive, I can make a decision in an hour over changes to orders or to make more garments.”
Dakota cut management salaries but was not forced to shut any of its factories, said Leung, who saw stronger future in China, especially with its supply chain integration with Vietnam – and to a lesser extent with Cambodia – as well as position as the centre of textile R&D.
While China’s manufacturing base was advanced, it would take much longer to develop retail brands to compete with household western companies like H&M or Zara, Ali said, as the Chinese clothing retail industry was notoriously fragmented.
“It could happen but it would take three to five years,” he said.
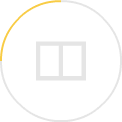