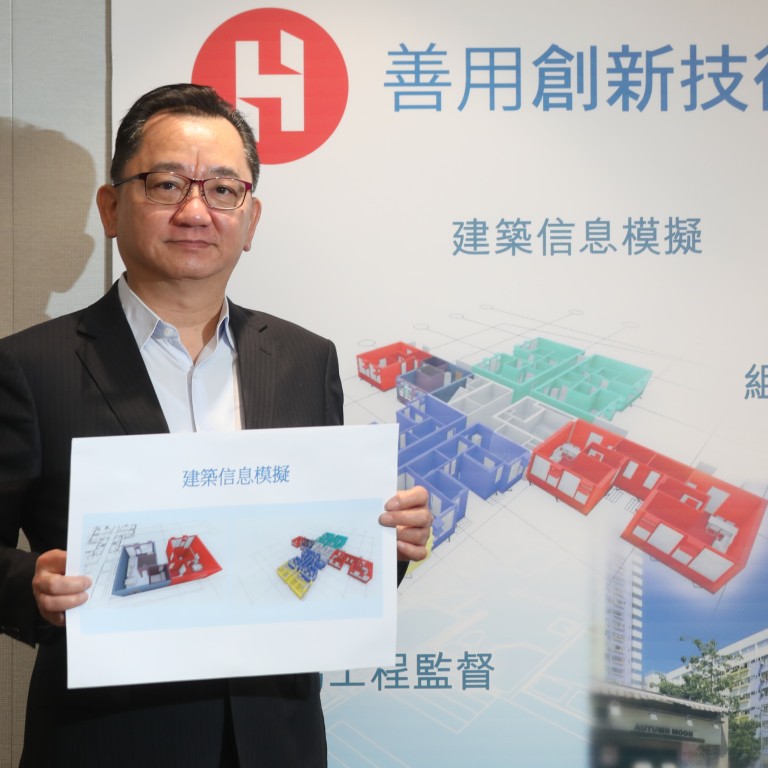
Hong Kong Housing Society tests ‘instant homes’ to speed up building flats at two projects
- Modular units are built in mainland China before being installed at project sites in Hong Kong
- Twenty-five-storey block of flats and 64-unit project, designed for elderly residents, will have prefab parts
The Hong Kong Housing Society is experimenting with a prefabricated construction method to shorten the time it takes to build new homes for two of its projects.
The society, the city’s second-largest public housing provider after the Housing Authority, plans to build 28,000 homes over the next decade.
It is testing the approach, known as “modular integrated construction” (MiC), at a 300-unit project at Hung Shui Kiu in the New Territories and a 64-unit project for elderly residents at Jat Min Chuen estate in Sha Tin.
The prefab technique involves making free-standing, integrated modules at a mainland Chinese factory. Once finished, they undergo quality inspections before being transported across the border to be installed at the project site.
Commonly used on the mainland, the method has been found to reduce construction time by 10 to 15 per cent, or about three months, compared to building at a site from scratch.
Chief Executive Carrie Lam Cheng Yuet-ngor urged the Housing Authority last October to adopt the MiC approach in more projects to quickly increase the supply of housing and shorten the long queue of applicants.
The Housing Society’s Hung Shui Kiu project will have 300 subsidised flats in a 25-storey block, expected to be completed in 2024. It will be the tallest building in the city constructed using the method.
“The project involves more than 1,200 components prefabricated in the mainland. We have to make sure there are no mistakes during the assembly process,” said Franki Yeung Kai-yu, the society’s project director.
Every prefab component had to be tagged, he said, so workers could use radio frequency identification (RFID) technology to check where each part was supposed to go and track both the transport and installation processes.
“By checking the tag, we’ll know immediately if a component is on the wrong floor or in the wrong flat,” Yeung added.
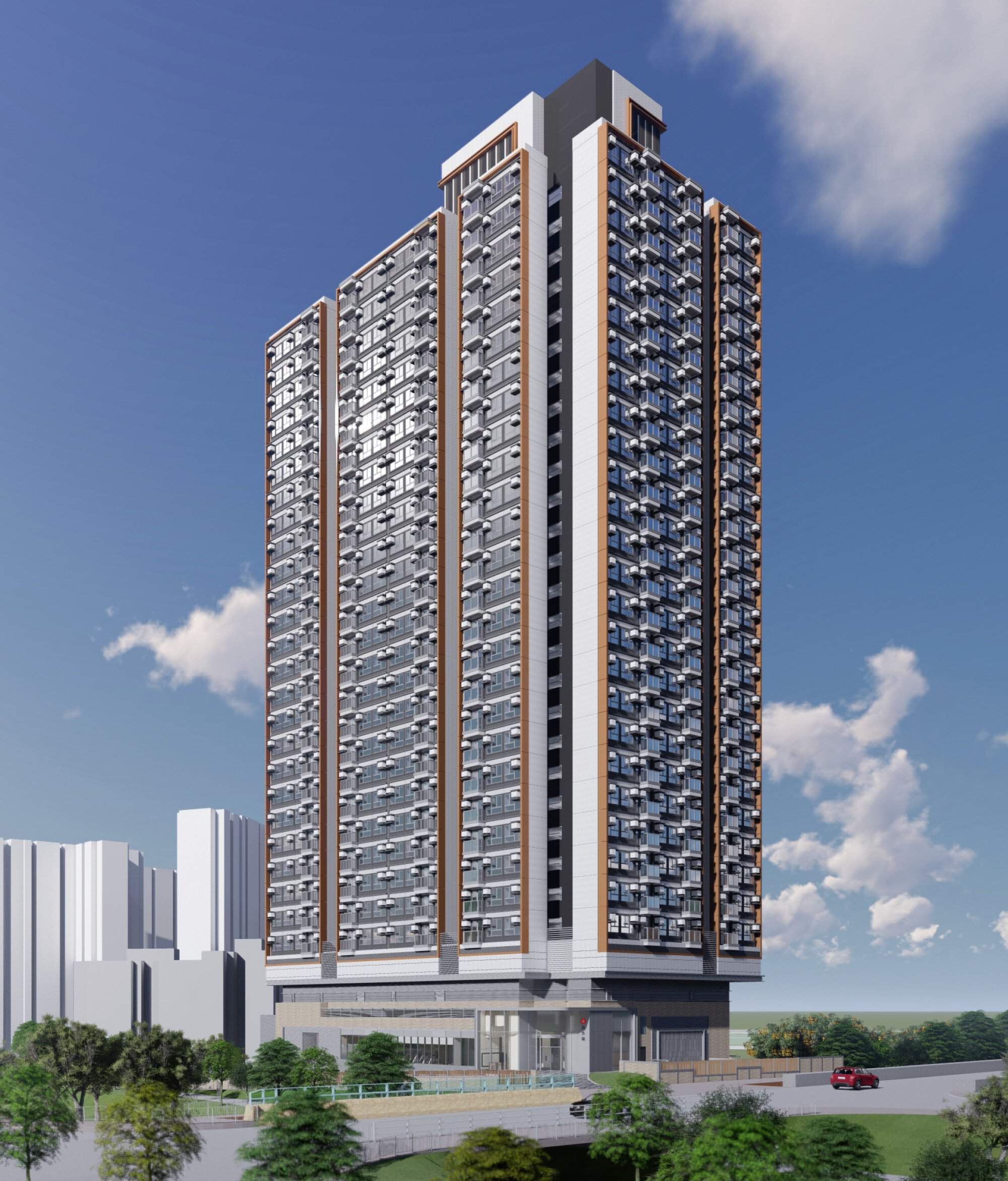
The society’s Jat Min Chuen estate project for seniors will have elder-friendly features such as extra-large entrances and doors to allow wheelchair access, and handrails along corridors and recreational facilities. It is expected to be completed by next year.
The society has also considered using the prefab method in other projects, such as at Kwu Tung North new town.
But Yeung said the method was not suitable for all projects because it was hard to arrange the transport and delivery of large prefab components weighing at least 20 tons. Not every construction site was suitable for it either.
The society, a non-governmental organisation that describes itself as the city’s “housing laboratory”, plans to build more than 40,000 subsidised homes over the next 20 years.
About 28,000 flats were expected to be completed over the coming decade, including at least 6,000 for new buyers and about 6,800 to be built as part of the redevelopment of existing estates.
More than 11,000 flats will go towards rehousing people affected by the government’s land clearance for redevelopment projects in urban areas.
In its efforts to ensure quality, the society has tweaked its system of awarding tenders to contractors.
It has begun weeding out bids considered to be much too low, as such behaviour could flag the risk of shoddy work and other quality issues.
After determining the midpoint of all bids received, it deducts points for all those below the median price. The society even considers disqualifying bids more than 50 per cent below the median level.
Yeung said the society was the first to adopt this system for assessing tender bids, adding that he believed it helped to set the standard expected from its contractors.
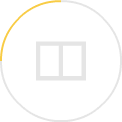